Изготовление крыла мотоцикла с нуля с чистого листа
Крыло мотоцикла с чистого листа.
Перед начинающими кастомайзерами при изготовлении чоппера, часто встаёт вопрос: где взять навеску для своего мотоцикла? А ещё чаще возникает вопрос: как её изготовить самому? И начинаются, как обычно, переделки из заводских мотоциклетных деталей. Режутся на куски стандартные баки, крылья, бардачки, и начинается добавление кусков металла и как всегда используется ведро шпаклёвки. В итоге эти детали обычно получаются чуть ли не в двое тяжелее оригинала, а вес, особенно для крыла, играет важную роль, так как при компоновке крыла с минимальным зазором от колеса получается прикольный вид, но в таком случае крыло нужно крепить уже не к раме, а к маятнику. И вот при таком креплении, тяжёлое крыло увеличивает неподрессоренную массу, что не лучшим образом сказывается на движении байка.
Можно конечно сделать деталь из стеклопластика, но если попробовать работать с ним, то оказывается возни с ним намного больше, чем с листовым металлом (проверено).
Ещё один большой минус таких переделок — одинаковость, это главная беда многих отечественных кастомов. Куда ни глянешь, везде видны фрагменты отечественных жестяных деталей, основная доработка которых, это расширение размера. Оно и понятно — многих останавливает недостаток информации и инструмента по работе с листовым металлом. В этой статье я постараюсь этот недостаток исправить, но опять же напомню, что описываться будет самое простое крыло, чтобы вам было легче понять технологию работы.
Я думаю хватит философии, пора заняться делом. Как обычно на любом заводе, изготовление качественной детали начинается с чистого листа бумаги. Так и мы, начинаем с чистого листа, а точнее картона. Вырезаем полоску картона длинной на ваше усмотрение. То есть вырезав полоску чуть длиннее чем нужно, примеряем к мотоциклу над колесом, и определившись с нужной длинной, отрезаем лишнее. А вот с шириной отпишусь немного поточнее. Для покрышки шириной 130 мм, ширина полоски картона должна быть на 40 мм шире и это для неглубокого крыла (какое вы видите на нижних фото). Значит нетрудно подсчитать ширину полоски для покрышки шириной аж на 360 мм: 360 + 40 = 400 мм. При обработке металл немного вытянется, но уверяю, не на много, к тому же немного ширины заберёт радиус загиба по контуру покрышки.
Определившись с размерами картонного шаблона крыла и перепроверив его на мотоцикле, закругляем (подрезаем) края полоски спереди и сзади (можно края подрезать более оригинально, чем на фото, я напомню это базовые знания) и переносим размер на миллиметровый лист металла (накладываем и обводим маркером). Затем вырезаем из листа металла нужную деталь болгаркой, ножницами, или электро-лобзиком, и заглаживаем кромки детали напильником или шлифовальным диском, убирая заусенцы.
Дальнейшая работа предстоит самая интересная: придание объёма плоской детали. Для этого потребуются: кожаная подушка, набитая песком или дробью (можно использовать дубовый пенёк с углублением в центре), и два самодельных молотка, со сферическими бойками. Один из них обычный (красный на фото) для начальной выколотки металла, а второй (чёрный на фото) понадобится для выколотки, когда крыло станет глубоким, и кромки его начнут упираться в ручку обычного молотка и мешать работе. Эти молотки я изготовил из шаровых опор грузовика ( у шаровых опор сталь качественная), а самый большой шар (сферу) на чёрном молотке, пришлось заказать токарю выточить из твёрдой стали. Сферические бойки молотков нужно обязательно отполировать до зеркального блеска.
Уложив металлическую листовую заготовку крыла на кожаную подушку, начинаем наносить частые равномерные удары сначала по центру листа, и плавно переходим к краям. При ударах лист будет стремиться свернуться вовнутрь, и это неплохо, так как нужно будет всё равно согнуть крыло по радиусу колеса, но при сильном сворачивании, деталь постоянно распрямляем и подправляем руками.
При выколачивании проверяем плавность закругления крыла (при виде спереди), а то может получиться так, что в центре радиуса закругления, крыло будет более выпуклым (острым), чем на краях. Значит нужно будет пройтись молотком ближе к кромкам по всей длине крыла, чтобы в итоге получить плавный радиус при виде спереди и сзади.
При выколачивании вы увидите, что постепенно глубина крыла увеличивается и здесь нужен другой молоток, так как кромки начинают упираться в ручку молотка и не дают нормально ударить. Нужно поменять молоток на другой (черный на фото) изготовленный с отдалённой рукоятью от сферического бойка.
Прикладывая деревянный шаблон, проверяем одинаковость выпуклости по всей длине.
Начинающим кастомайзерам, которые имеют небольшой опыт работ с листовым металлом, бывает трудно добиться одинакового профиля (выпуклости) крыла по всей длине. Таким людям я советую пользоваться деревянным шаблончиком из дерева (смотрите фото слева), прикладывая который по всей длине крыла, вы сможете проверять одинаковость выпуклости по всей длине.
Что касается радиуса крыла при виде сбоку (то есть радиуса самого колеса) то тут всё немного сложнее. При выколачивании металла, в середине крыла появляется выпуклость и металл растягивается, но с боков (ближе к кромкам) мы удары не наносим и металл остаётся каким был — более толстым, чем в середине.
Для облегчения процесса и придания нормальной формы крылу (без волн на боковинах крыла) нужно листовой металл на боковинах крыла сжать, то есть сделать металл на боковинах (кромках) крыла ещё толще. Для этих целей обычно применяют шринкель, но он есть далеко не у всех. Я предлагаю более древний и простой вариант, которым пользовались ещё при изготовлении рыцарских доспехов. Нужно по всей длине обоих боковин выдавить гофры (см. фото) и при их выдавливании вы увидите, что крыло само начинает уменьшать свой радиус. Гофры нужно выдавить так, чтобы радиус крыла стал намного меньше радиуса колеса (если диаметр колеса на 16 дюймов, а радиус естественно 8 дюймов, то диаметр крыла с гофрами должен получиться примерно на 12 дюймов, а радиус соответственно всего 6) и далее объясню для чего это нужно.
Дело в том, что теперь, чтобы сжать (сделать металл толще) боковины крыла, нужно эти гофры выровнять ударами молотка или специальной лопатки (см. фото). Нанося удары на гофры на выпуклой наковаленке, мы одновременно и выравниваем боковины от уже ненужных гофров, и одновременно сжимаем и утолщаем листовой металл, так как при выравнивании гофров, от ударов идёт наволакивание металла и его одновременное сжатие по длине и утолщение листа по толщине — так называемый наклёп металла. Но при этом процессе опять идёт увеличение радиуса крыла (крыло постепенно выпрямляется), и именно для этого я и написал выше, для чего нужно сделать радиус крыла с помощью гофрирования намного меньше, чем радиус колеса.
В итоге нужно добиться, чтобы радиус крыла совпал с радиусом колеса (при работе крыло постоянно прикладываем к колесу), и процесс гофрирования и обстукивания (выравнивания и наклёпа) боковин иногда приходится сделать пару раз, а на более глубоком крыле бывает и три-четыре раза.
Но это довольно быстрый процесс, если сделать специальную гофрилку из любого небольшого прессика (см, фото и видео чуть ниже). Если нет пресса или нет времени возиться (я потратил на изготовление всего день), то можно сделать простую гофрилку из двух штырей (прутков) диаметром 8 — 10 мм, приваренных рядом друг с другом на расстоянии пару мм (типа вилки).
Про шринкер и стретчер желающие могут почитать вот в этой статье.
С этим устройством работа пойдёт немного медленнее, так как чтобы сделать одну волну (гофру), придётся поместить кромку крыла между штырей и затем провернуть крыло между ними и отодвинув его дальше (по длине) примерно на сантиметр опять провернуть. Но работать вполне возможно и привыкнув можно увеличить скорость гибки.
При желании можно сделать более глубокое крыло (см. фото справа), если ещё раз пройтись по всему крылу частыми ударами, но тогда общая ширина крыла может уменьшится и крыло станет глубже но тоньше по ширине.
После нанесения гофров, их выравнивания и подгонки радиуса закругления крыла к радиусу колеса (об правильном изготовлении самодельного мотоциклетного колеса, но с заводской технологией, можно почитать вот здесь), всё равно могут остаться небольшие волны на кромках крыла, но это уже мелочи и исправляются они обстукиванием на выпуклой наковаленке.
Подровняв по кругу кромки крыла, переворачиваем крыло выпуклой стороной вниз, и уложив его на плоскую гладко-шлифованную наковальню (фото её можно увидеть в этой статье про изготовление бака), обстукиваем изнутри всё крыло пластиковой киянкой, с сферической поверхностью ударной части. Это нужно, чтобы немного подровнять шишки на металле, и ускорить прокатку на английском колесе. Впрочем у кого мощное и большое английское колесо, и есть опыт работы с этим станком, то операцию обстукивания на плоской наковальне можно не применять.
Остаётся одна из самых интересных операций — прокатка крыла между роликами английского колеса, и превращение мятого и невзрачного куска металла в гладкое и привлекательное изделие, для которого перед покраской не требуется ни грамма шпаклёвки. Процесс прокатки описывать не буду так как он не сложен и начав прокатывать деталь, научится можно через пару часов тренировки. К тому же немного об этом я написал в статьях про бензобаки. И уверяю вас, что работая на этом станке, вы с каждым днём и довольно быстро будете открывать новые, более удобные для вас методы работы без всяких подсказок. Это станок который надо почувствовать и советы здесь бессмысленны. Скажу только одно — на первых порах работы, держите пальцы подальше от роликов, так как усилие от скобы может составлять несколько тонн.
После прокатки крыла на английском колесе, можно ещё раз подравнять волны на кромках крыла (если они есть), обстукиванием на выпуклой наковаленке по периметру всего крыла, а можно чуть загнуть кромку, по периметру нанося более сильные удары и держа кромку немного под углом к наковальне. Это сделает крыло жёстче. При необходимости, кромки можно снова прокатать на колесе. Кстати о жёсткости: кому посчастливилось изготовить или купить станочек, называемый зиговочная машинка, то подобрав в продаже или выточив на станке специальные ролики, можно завернуть кромку крыла во внутрь, прокатав между роликами всё крыло по периметру. Это придаст изделию красивый законченный вид и дополнительную жёсткость. О зиг-машинке можно почитать здесь, но у кого её нет, можно аккуратно приварить по периметру кромки крыла проволоку (изнутри), диаметром 4 — 5 мм, тем самым добавив жёсткость крылу и более достойный вид.
Способов креплений крыла множество. Можно приварить аккуратные ушки с отверстиями к крылу и к ним добавить стойки, а можно аккуратно просверлить отверстия в крыле, а к отверстиям прикрепить стойки с помощью заклёпок или болтов. Есть неплохой способ крепления крыла когда стойки, держащие крыло, выполнены из крученного квадратного прутка и продолжаются вверх, образуя спинку — сисибар. Этот вариант часто используется в шведской школе кастомайзинга. Несомненно выбирать вам, и большая возможность выбора является одним из главных приколов кастомайзинга.
Тем мастерам, для которых на первом этапе тяжело приобрести или изготовить станок английское колесо, посоветую изготовить крыло для мотоцикла без использования английского колеса. Как это осуществить, можно узнать кликнув вот по этой ссылке.
И последнее. Чтобы заказать крыло для кастома из каталога, придётся выложить около 300 долларов, а за крыло для покрышки на 360 мм — ещё больше. Но при самостоятельном изготовлении, вы потратите за кусок листового металла цену около 1 доллара и получите кучу положительных эмоций. Как говорилось в какой то рекламе — почувствуйте разницу. Но не это главное: изготовив крыло для мотоцикла своими руками, вы получите изделие в единственном экземпляре и что самое главное — гордость за себя, а это поверьте дороже денег. Успехов всем!
Изготовление матриц для передних крыльев
На данный момент все популярнее становится тюнинг и облегчение кузова автомобиля. Так же если вы обладаете достаточно старым автомобилем, то некоторые фрагменты кузова очень сложно достать, или же они будут стоить просто баснословные суммы денег. На первый взгляд, это является очень затратной частью, но ничего страшного в этом нет, ведь вы всегда можете сделать не большой custom своими руками.
Мы расскажем с помощью чего, можно сделать при минимальных затратах новые передние крылья не уступающие по прочности заводским аналогам.
С чего же начать?
- Первым этапом в постройке матрицы передних крыльев является выведение первоначальной формы крыла. Если есть неровности, вмятины, проржавевшие места, все это необходимо выровнять, за шпаклевать, и вышкурить, добиться максимального эффекта к заводским параметрам.
- Обклеиваем окантовку металлическим скотчем или плотным картоном
- Наносим втирая на нашу поверхность воск с помощью губки (данный этап проводится в 3-4 слоя с промежутком высыхания 1 час)
- После высыхания последнего слоя накладываем матричный гелькоут(наносится в 2 слоя с промежутком 20-25 минут. После чего необходимо отстоятся 4 часа для полного высыхания)
- Наносим слой стекловуали(тщательно укладываем и промазываем все неровности,впадины и изгибы что бы не образовалось пористого места)
- Наносим 2 слоя стекломата 300 с промежутком слоя 1 час и затем 600 с промежутком слоя 1 час.
Даем высохнуть 5-6 часов.
- Что бы предать матрице более плотную форму и избежать деформации или поломки самой матрицы, необходимо сделать каркас жесткости. Для использования каркаса можно использовать деревянные доски
- Подгоняем доски под наше крыло,скручиваем саморезами для прочности и заливаем несколькими слоями с промежутком 1 час стекломат 600
После чего даем пару дней полностью высохнуть изделию. - После высыхания, обрезаем лишние края и аккуратно извлекаем деталь из матрицы.
Матрица передних крыльев готова
Источник: DRIVE2
Понравилась статья? Поделить с друзьями:
Приложение — Коммерсантъ Авиастроение (102728)
Для изготовления углепластикового крыла и хвостового оперения российского среднемагистрального самолета МС-21 использована новейшая инфузионная технология, позволяющая серийно производить консоли крыла большого удлинения. Кроме того, использование так называемых композиционных материалов в конструкции воздушного судна позволит увеличить его ресурс, повысить безопасность и сократить расходы на изготовление и техобслуживание.
Материальные ценности
Каркас крыла своего первого самолета Flyer-1 братья Райт изготовили из ели, обтянув его тонким небеленым муслином. С помощью этой конструкции 17 декабря 1903 года и были совершены первые в истории задокументированные полеты аппарата, поднявшегося в воздух с помощью тяги двигателя. Скоро для большей прочности вместо ткани в ход пошли фанера или деревянный шпон. Однако уже 12 декабря 1915 года в воздух поднялся первый в мире цельнометаллический самолет — моноплан Junkers J.1. В 1920-1930-е годы в конструкции самолетов во всем мире вместо древесины стали применять алюминий. Он позволял самолетам летать с большей скоростью и полезной нагрузкой.
«70 лет назад, в конце 20-х — начале 30-х годов прошлого века, человечество перешло при постройке самолетов от дерева к металлу. Сейчас идет массовый продуманный переход от металла к композиту,— говорит директор Центрального аэрогидродинамического института им. профессора Н. Е. Жуковского (ЦАГИ) Сергей Чернышев. — Применение композитов имеет целями: снижение веса конструкции самолета на 15-20%, повышение ресурса в полтора-два раза, повышение безопасности по прочности в несколько раз, сокращение сроков разработки и производства при одновременном снижении стоимости изготовления и расходов на техническое обслуживание и ремонт». В 80-е годы прошлого века в авиации началась «композитная революция»: в элементах конструкции сначала военных, а потом и гражданских самолетов все чаще стал использоваться углепластик. До авиастроения он уже использовался в середине 60-х годов прошлого века в военных и космических программах. Из этого материала делали сопла ракет и шлемы астронавтов.
В 1967 году углепластик появился в свободной продаже в Англии, а первым известным гражданским применением такого композита стал корпус болида команды «Формулы-1» McLaren, изготовленный в 1981 году Джоном Барнардом. А сегодня углепластик входит в наш быт: из него сделано множество вещей. Однако технологические тонкости их изготовления остаются одной из самых охраняемых тайн любого производителя.
Использование композитов в авиации началось с военных самолетов. Композиты позволили снизить массу летательного аппарата, повысить его ресурс, а значит, увеличили его тактико-технические характеристики. Сначала из углепластика делали небольшие лючки, обтекатели. Затем пришла очередь элементов конструкции крыла — закрылков, предкрылков. Сегодня доля композитов в конструкции истребителей пятого поколения составляет от 40% до 60%.
Доля композиционных материалов в конструкции пассажирских самолетов тоже постоянно росла. Например, в моделях семейства А320 компании Airbus, разработанного в середине 80-х годов прошлого века, она составляет 10-15%. У двухэтажного А380, спроектированного в конце 1990-х годов, композиты составляли 25% общей массы лайнера. Boeing 787 Dreamliner на 50% состоит из композитов, A350 — на 53%.
Пластик в авиации
Углепластик изготавливают из слоев ткани, сотканной из тончайшей углеродной нити. Классическая технология выглядит так: на специальную оснастку слой за слоем выкладывают углеродную ткань, предварительно пропитанную связующим веществом (смолой). Затем полученную заготовку помещают в автоклав — большую печку, где под воздействием высокой температуры происходит «выпекание» изделия. После охлаждения конструкция становится монолитной. По такой автоклавной технологии изготавливаются элементы конструкции европейских и американских самолетов. Причем отдельно делаются заготовки для силового набора, отдельно — обшивка, и потом они собираются в единую конструкцию.
Теоретически такая технология должна привести к сокращению массы планера самолета на 15%. На практике это преимущество пока удается реализовать не полностью. Причина — исключительно высокие требования к надежности пассажирских самолетов на фоне не очень большого опыта эксплуатации конструкций из композиционных материалов.
«При проектировании конструкции из алюминия запас прочности сейчас не превышает 1,5,— рассказывает директор технологического центра Объединенной авиастроительной корпорации (ОАК) Юрий Тарасов.— При проектировании же конструкции из углепластика поначалу этот запас нередко доходил до 5 или даже 7 (это означает, что конструкция рассчитывается и испытывается на нагрузки, в пять-семь раз превосходящие максимальные эксплуатационные). По мере набора статистики поведения композитов запасы прочности постепенно снижаются, конструкции из них получаются все более легкими».
Композиты — дорогое удовольствие: килограмм дюраля для самолета стоит около $3, а килограмм углепластика, из которого изготавливались крыло и фюзеляж Boeing B787,— примерно $400. Но использование более дорогого материала окупается его уникальными свойствами. «Расход топлива на Boeing 787 за счет снижения веса уменьшился практически на 20%, эксплуатационные расходы — на 10%,— говорит Борис Бычков, генеральный директор компании Airclaims CIS, специализирующейся на экспертизе и техническом аудите в области авиастроения.— Кроме того, от воздушных судов клепано-алюминиевых конструкций Boeing 787 отличает отсутствие коррозии, что значительно облегчает обслуживание самолета».
Начало применения в авиастроении нового материала, естественно, не было простым. Во время первых испытаний элементов новых самолетов возникали неожиданные трудности. Так, в конце марта 2010 года в исследовательском центре Эверетт во время испытания углепластикового крыла Boeing 787 на излом обнаружилось отслоение композитной обшивки от стрингеров. Больше полугода инженеры Boeing занимались устранением проблемы. Дальнейшие испытания самолет прошел успешно.
В марте 2014 года на крыльях нескольких новых B787 были обнаружены микротрещины. Дефекты начали появляться после внесения подрядчиками изменений в технологический процесс. Проблема была выявлена на нескольких самолетах, которые еще не успели передать заказчикам. Техпроцесс был скорректирован, после чего микротрещины больше не появлялись.
Опыт первых композитных конструкций заставил усовершенствовать систему контроля качества. Заводы обзавелись установками неразрушающего контроля, которые позволили выявлять микротрещины на этапе производства. По оценке специалистов, контрольно-диагностические системы, которые сегодня используются российской компанией «Аэрокомпозит»,— одни из самых совершенных в мире. Именно она и отвечает за производство «черного крыла» МС-21.
Развитие диагностических технологий позволяет решить еще одну проблему: выявление и устранение повреждений, которые могут возникнуть при эксплуатации. Для авиакомпаний и сервисных центров это новая задача. Однако в истории авиации радикальные изменения в технологиях ремонта уже происходили. Самолеты, сделанные из дерева и полотна, ремонтировали квалифицированные столяры. Внедрение в авиастроение металлов заставило освоить сварку, клепку и пайку. И тогда это не всем нравилось, однако возврат к деревянно-полотняным технологиям в качестве серьезной альтернативы не рассматривался.
«У композитов есть очень серьезные преимущества по сравнению с металлами,— считает гендиректор Инженерного центра Airbus в России Александр Кирейцев.— Металлические самолеты подвержены усталостным разрушениям, поэтому их проектируют на определенное количество циклов. Композиционные материалы гораздо более устойчивы к знакопеременным нагрузкам и не подвержены коррозии, поэтому они долговечнее металлов. В долгосрочной перспективе у меня нет сомнения в росте процента использования композитов».
Для производства крыла самолета МС-21 было принято решение использовать новую безавтоклавную технологию. «Для МС-21 мы создали композитное крыло более совершенной аэродинамической формы. Нашими специалистами был разработан метод вакуумной инфузии, который позволяет нам создавать силовые элементы консоли крыла лайнера интегральными»,— говорит генеральный директор компании «Аэрокомпозит» Анатолий Гайданский. Автоматизированный комплекс выкладывает преформу набором из 24 шестимиллиметровых углеродных лент слой за слоем, затем конструкция помещается в вакуумный мешок, где пропитывается связующим (смолой). Далее в специально спроектированной печи при относительно невысоких температурах происходит процесс отверждения. Таким образом можно получать монолитные элементы длиной до 20 м, что является совершенно уникальной технологией в мире. «У нашего крыла высокое аэродинамическое качество. Аналогичную конструкцию консолей крыла самолета из алюминия сегодня изготовить нельзя»,— отмечает Анатолий Гайданский. По его словам крыло большого удлинения позволит добиться для МС-21 снижения расхода топлива до 8%.
За жизненный цикл самолет тратит очень много топлива, так что это станет его серьезным конкурентным преимуществом.
Только за счет «черного крыла» на каждом таком самолете можно было бы сэкономить более 11 тыс. тонн горючего! А если в парке авиакомпании больше сотни самолетов, то экономия более чем впечатляющая.
Отечественные технологии
В российском авиапроме, как и в западном, композиционные материалы применялись сначала в основном в производстве военных самолетов, а в конструкции гражданских лайнеров из углепластика изготовлялись лишь элементы механизации крыла, лючки и обтекатели. Но иностранные производители существенно увеличили долю композитов в конструкциях гражданских самолетов, в России же до недавнего времени этого не делали. Например, доля композиционных материалов в самолете Sukhoi Superjet 100 составляет около 12%. Это объяснялось в том числе слабыми производственными возможностями и недостаточным технологическим развитием производителей композитов в нашей стране.
Однако конструкторы КБ им. А. С. Яковлева (подразделение корпорации «Иркут») при разработке самолета МС-21 решили использовать крыло из углепластика для обеспечения конкурентоспособности новой машины на мировом рынке. Почему только крыло? Анализ показал, что фюзеляж среднемагистрального самолета такой размерности делать из композитов невыгодно.
На начальном этапе создания композитного крыла была проделана большая подготовительная работа. Было изготовлено и испытано в ЦАГИ больше 5 тыс. элементарных и конструктивно подобных образцов. Для проведения статических и ресурсных испытаний изготовили четыре прототипа кессона крыла. Первый этап испытаний завершился в конце 2011 года. На основании его результатов было установлено, что полномасштабные силовые конструкции, получаемые методом вакуумной инфузии, не хуже, чем автоклавные, с точки зрения прочности и точности геометрии. В итоге было принято решение о принятии этой технологии изготовления элементов композитных конструкций и об использовании определенного композиционного материала.
Параллельно с работой в ЦАГИ в компании «Аэрокомпозит» была организована опытная лаборатория. Возглавил ее Алексей Слободинский (сейчас — генеральный директор производственной площадки «КАПО-Композит» в Казани).
«Создание лаборатории на начальном этапе было обусловлено необходимостью исследования композиционных материалов и отработки технологии изготовления на их основе опытных образцов. По сути, была создана лаборатория, которая помогла в запуске новой производственной площадки в Ульяновске, дала возможность смоделировать применение метода вакуумной инфузии и проверить заложенные конструктивные и технологические параметры»,— рассказывает Алексей Слободинский.
«Компания Boeing на самолете B787 уже сделала композитное крыло, Airbus создал такое же крыло для самолета А350,— говорит Юрий Тарасов.— Однако в них присутствуют практически те же элементы, что и в металлическом крыле. То есть радикального изменения трудоемкости сборки не произошло. Создавать новое крыло для МС-21 с оглядкой на устаревшие решения было бы нецелесообразно в принципе. В этом случае мы всегда будем догонять лидеров и вряд ли вырвемся вперед. Поэтому мы поставили задачу сделать следующий шаг — перейти на безавтоклавную технологию. Сейчас такие технологии начали применять лишь на отдельных западных предприятиях».
С целью вывода российского авиапрома на принципиально новый научно-технический и производственный уровень ОАК создала ряд специализированных центров компетенций, одним из первых стала компания «Аэрокомпозит». В команде опытные конструкторы, прочнисты, технологи. Производство располагается на заводах в Ульяновске и Казани. В Москве находятся опытная и испытательная лаборатории. В Казани изготавливают панели носовой и хвостовой частей консоли крыла, законцовки, элементы механизации и управления. В Ульяновске производят силовые элементы конструкции консоли крыла: панели кессона крыла, лонжероны, дренажные короба, а также панели центроплана. Для обеспечения контроля качества элемента при его изготовлении параллельно изготавливается изделие-спутник из той же партии углеродного наполнителя и по тем же параметрам, что и основной элемент. Далее изделие-спутник делится примерно на 600 образцов, которые проходят испытания. И только после положительного заключения композитный элемент конструкции перемещается на следующий производственный участок.
Новые материалы позволят обеспечить ресурс конструкции планера самолета более 80 тыс. летных часов, что почти в три раза больше, чем ресурс современных самолетов — 20-30 тыс. летных часов. При этом масса конструкции уменьшится примерно на 30%. Новые материалы позволят создавать умные конструкции, адаптирующиеся под определенные условия и даже самовосстанавливающиеся.
Константин Лантратов
Как сделать пластиковые крылья самолету своими руками
Выбор проекта в пользу KR2S пал не просто так. В начале 2006 года мой коллега и я планировали построить полнопилотажный тренажер самолета, поскольку оба были фанатами MS Flight Simulator. Харди, по профессии инженер, имел талант находить старым вещам новое применение. Так мертвый видеомагнитофон и двигатель от стеклоочистителя могли стать основой для системы подвижности авиатренажера. Но после небольшой прикидки на размер бюджета мы выяснили, что стоимость нашей задумки может превысить 10000$.
Во время поисков информации в Интернете на тему подвижных авиатренажеров, я случайно наткнулся на статью о самолете стоимостью в 10000$. Это был KR2S, и эта была любовь с первого взгляда. Именно этот самолет я мог сделать своими руками, он стоил меньше симулятора и мог помочь мне продолжить мои летные уроки.
Кроме характеристик и внешнего вида самолета, меня привлекло сообщество KR строителей, которое располагала к себе в плане помощи решения сложных вопросов во время строительства. Всегда можно было рассчитывать обратиться за поддержкой к тем, кто уже прошел этим путем.
KR2S, задуманный мной, был маленьким самолетом с хвостовым колесом и с ламинированным гнутым лонжероном. На страницах этой статьи вы найдете описание опыта постройки этого самолета, вместе с полезными советами решения разных задач. И это будет моя версия того, как построить Rand Robinson KR2S.
Так описывает начало своего увлечения строительством самолёта Дарен Клутенг-Кромптон из Австралии, оригинальную подборку статей которого на тему строительства KR2S можно найти на английском языке на сайте www.kr-2s.com.
Формирование стеклопластиковой обшивки крыла
Центральная часть крыла крепится непосредственно к фюзеляжу самолета. К двум лонжеронам, выходящим из фюзеляжа, крепится консоль крыла и все остальные его элементы. Внутреннее пространство между лонжеронами и нервюрами позволяет разместиться топливному баку, узлам управления и проводке навигационных огней. Наружная обшивка формирует профиль крыльев, предохраняет органы самолета от повреждения, а также создает прочностную основу самолета, поэтому к её изготовлению следует подойти внимательно.
Толщина обшивки крыла определяется по заранее построенным контурам на нервюрах. В данном случае линия 3/8” определяет контур будущей обшивки. На фотографии скреплены с помощью степлера два шаблона нервюр: с хордой 44″ (дюйма) и с хордой 48”. По этим контурам определяется толщина наружной обшивки.
Внутрь крыла, отмеченного лонжеронами и нервюрами, кладется кусок пенопласта толщиной 2”. После чего края пенопласта срезаются по границам контуров на нервюрах.
Пенопласт затем извлекается, а по отмеченной линии рубанком аккуратно срезаются излишки пенопласта.
Процесс выполняется до получения ровной поверхности.
Так, что после установка обшивки, её границы точно соответствуют границам ранее отмеченных контуров на шаблоне, в данном случае 3/8”.
Предварительная подготовка места под укладку слоя обшивки включает в себя подвязку ремней, чтобы обшивка не упала на гаражный пол, а также изоляцию места монтажа полиэтиленовыми пакетами для улучшения адгезии.
Стеклоткань заготавливается вне места укладки. Заготовкой служит простой стеклотканевый лист. Кстати, стеклоткань кладется на пенопласт под углом 45° по направлению хорды крыла.
Такой сэндвич затем помещается внутрь крыла и предохраняется ремнями от падения. Также можно использовать дополнительные пластины, бруски из дерева и прижимы.
Установка топливного бака
После полимеризации и извлечения «пирога», с лонжеронов были сняты шаблоны нервюр. Для облегчения нервюр на шаблонах с помощью дрели с насадкой было сделано несколько отверстий, при этом было обеспечено достаточное минимальное расстояние между отверстиями и кромками крыла в пределах 1,5” для прочности. После этой операции нервюры стали весить на 280 граммов легче.
Ширина углубления на шаблонах оказалась не достаточной для установки на лонжероны, так что лонжерон пришлось зашкурить.
После монтажа обшивки на место, приходит самое время для изготовления опор топливного бака. Опоры приклеиваются эпоксидной смолой с наполнителем к обшивке.
Интересная операция выполняется перед монтажом бензобака на опоры: на опоры топливного бака между ним и бензобаком временно кладется наждачная бумага.
Топливный бак помещается сверху на обшивку и фиксируется в этом положении, после чего наждачная бумага извлекается. Данная процедура позволяет подогнать контуры опор под основание бензобака.
Сверху на пенопластиковые ребра помещается очередной слой стеклоткани с небольшим содержанием эпоксидной смолы. В тех местах, где слой не сажается до конца, пенопласт дорабатывается. После полимеризации кромки и углы ребер становятся по-настоящему крепкими.
Прежде чем использовать стеклоткань для крепления нижней обшивки, каждый лонжерон был обмазан клеем в трех местах. Это укрепило место установки топливного бака перед монтажом обшивки на длительное время.
Установка топливного бака была выполнена также по шаблону.
Стеклоткань кладется на внутреннюю часть обшивки стандартным способом, а жертвенная ткань лежит сверху, чтобы впитать излишки смолы. Вся операция выполняется на верстаке, а время сушки примерно час. Стеклопластик довольно липкий и податливый, поэтому, когда обшивка переворачивается, она все ещё остается достаточно мокрой, чтобы прилипнуть к слою жертвенной ткани. Как только форма обшивки сформирована, верхняя часть все еще остается плоской. Чтобы отвердевание прошло успешно сверху кладется доска и зажимается струбцинами.
Как только внутренняя часть обшивки отвердевает наступает время добавить еще несколько слоев стеклоткани, как и в случае с нижней обшивкой. Это поможет прочно зафиксировать топливный бак в продольном направлении крыла.
Так выглядит внутренняя часть верхней обшивки с установленными ребрами жесткости в продольном направлении крыла.
Изготовление носовой кромки
Чтобы собрать носовую кромку достаточно 2 кусков 2” пенопласта, которые собираются в секцию по контурам нервюр от 3/8” до ½”. Получается пакет V-образной формы.
Крепежные узлы на лицевой стороне переднего лонжерона закрываются изолентой.
Однослойный кусок стеклоткани помещается внутри передней кромки из пенопласта. После сглаживание морщин в жертвенной ткани концы пакета скрепляются степлером для того, чтобы кусок стеклопластика оставался прочным. Далее вся конструкция оставляется на час, чтобы стеклопластик прочно прилип к пенопласту.
Через час передняя кромка устанавливается в нужное место напротив основного лонжерона, пока не отвердеет окончательно.
Лишний пенопласт необходимо ободрать рашпилем и зачистить шкуркой по шаблону.
Один из вариантов -ободрать пенопласт с передней кромки, для этого можно использовать асфальт.
Вот так выглядит центральная часть крыла после зашкуривания. В целом поверхность можно доработать шкуркой до идеальной формы или близкой к ней.
Контуры листа стеклоткани под вырезание отмечаются прямо по форме передней кромки.
Ночи бывают холодными, и вырезанный кусок стеклопластика плохо будет абсорбироваться с жертвенной тканью на утро. Для того чтобы его согреть и сделать более податливым, можно использовать 500 Вт лампу.
Утром сэндвич из стеклоткани и жертвенной ткани кладется на переднюю кромку, предварительно установленную по месту.
На следующий день сэндвич легко снять, если заранее побеспокоится о применении клейкой ленты. Доводку передней кромки можно оставить до момента завершения строительства крыла.
Изготовление хвостовика и его обшивки
Хвостовик крыла также формируется с помощью слоенного пирога. В качестве основы используется вырезанный по шаблону кусок пенопласта. Его поверхность должна получиться ровной без изъянов от начала до конца.
Обе внутренние поверхности, формирующие хвостовик, будут состоять из одного слоя стеклоткани.
Лучший вариант по вопросам удобства – приклеить шаблоны вместе с сосновыми клиньями. Такая конструкция жестко устанавливает размер.
Поскольку данная деталь будет закрылком, удобнее изготовить её отдельно от остальных. При монтаже она устанавливается вдоль контура ½” с помощью струбцин и раздвижного зажима. Низ подвижной створки зачищается по шаблону.
Острая кромка также зачищается по шаблону.
Эпоксидный клей и углепластик также наносятся на пенопласт. Операция выполняется на рабочем столе: всё фиксируется и остается сохнуть на два часа. Так что пластиковая обшивка не будет слезать, но в то же время останется достаточно податливой, чтобы позже её можно было выравнять.
На фото снизу также можно увидеть алюминиевый уголок, стеклоткань вместе с жертвенной тканью.
Откидная крышка также будет вращаться на рояльных петлях.
Так закрылок будет выглядеть в нижнем положении.
Процесс ошкуривания пенопласта до толщины 3/8” начинается с покрытия обеих сторон эпоксидной смолой. После ряда подобных операций пластинка становится очень твердой и легко обрабатываемой.
Поверхность закрылка укреплена диагональным ребром жесткости, это сделано для того, чтобы уменьшить любое торсионное скручивание при вращении. В то время как у кого-то может возникнуть желание облегчить конструкцию за счет дополнительных ребер жесткости, было принято решение также усилить составной бандаж в центре дополнительным ребром с креплением к лонжерону.
После работы над закрылком приходит время заняться установкой топливного бака и его подключением к топливной системе.
Если перебрать с наполнителем, то можно увидеть, как пена, похожая на тесто, будет лезть из всех щелей, а сам процесс извержения может затянуться до 30 минут. Что касается наполнителя, то его можно приобрести в строительных магазинах. Для бензобака может наполнитель для утепления крыш под маркой DIVINYCELL.
На этом этапе должно также состояться ваше знакомство с проводкой. От топливного бака необходимо будет провести провода: красный с положительным зарядом и белый провод с отрицательным. Для фиксации проводов используются либо кабельные фиксаторы, либо жидкие гвозди.
Расширяющийся наполнитель некоторое время будет просачиваться в промежутке между топливным баком и задним лонжероном, так что понадобиться мелкий рашпиль и около 45 минут работы для надежного удаления излишек.
Прежде чем установить заднюю обшивку на место, все болты и гайки стоит затянуть и покрыть эпоксидной смолой в качестве «контровки».
Это верхний слой обшивки с мокрыми углеродными волокнами. Он готов к перевороту и применению на лонжеронах и фанерных профилях.
Внутренняя часть верхней обшивки покрывается эпоксидным клеем в местах сопряжения с лонжеронами.
Доделка проекта
Основная обшивка была отягощена преднамеренно деревяшкой и куском рельсы для того, чтобы остановить «кипение пены» и возможного поднятия обшивки. Если внимательно присмотреться, то можно увидеть, что из горловины бака торчит ручка. Она облегчит снятие обшивки, когда процедура будет завершена.
Через сутки профиль зашкуривается наждачной бумагой, закрепленной на доске, размерами 4” на 1”.
Съемная трубка Пито выглядывает наружу из-за передней кромки. В том месте пенопласт был удален и вместо него был приклеен кусочек древесины. В кусочке дерева есть просверленное отверстие, куда вставляется трубка для замера скорости. Вокруг трубки лента для адгезии, так что смола не будет липнуть.
Вот так выглядит передняя кромка сзади: кусок древесины с просверленным отверстием посередине и трубка ПВХ, впаянная в это отверстие.
От датчика скорости идет воздушная трубка диаметром 5/8”, опоры которой вмонтированы в переднюю кромку.
Количество навигационных огней к моменту написания статьи не было известно точно, поэтому были проведены три пары проводов 16G Tefzel и одна пара 14G. Одна пара 16G используется для датчика топливного бака, другие две идут на стробы (на законцовках крыльев огни против столкновений) и навигационные огни. Все провода идут к блоку, смонтированному на главном лонжероне. Они промаркированы лентами разного цвета на концах.
ПВХ трубки защищают провода от истирания в отверстиях через ребра жесткости или фюзеляж. Каждый раз, когда провода находятся в соприкосновении с металлическими частями, они изолируются дополнительными ПВХ трубками или резиновыми прокладками.
На фотографии запечатлен момент установки передней кромки на лонжероны и нервюры. Самолет KR вывезен из гаража и перевернут вверх тормашками. Для окончательного приведения в норму поверхности были еще раз ошкурены и очищены пылесосом.
Сходный процесс изготовления обшивки используется для низа самолета. Прежде всего, в пластике делается прорезь для установки стойки посадочного колеса. Поскольку передняя кромка уже покрыта одним слоем пластика, второй слой ложится сверху и выпирает над 2 дюйма над первым. То же самое происходит с обшивкой, итого крыло становится толще на два слоя, по 2 дюйма с каждой стороны. Крыло становится практически неразрушимым для камней, насекомых и вездесущих животных.
При разметке стеклоткани следует дополнительно маркировать листы фломастером для предотвращения ошибок.
Как и в случае с задней кромкой прежде нужно дождаться, когда займет все щели.
После того, как обшивка высохнет в течение 3 часов, передняя кромка прокалывается шплинтом и болтом AN4 в месте вентиляции топливного бака и трубки Пито.
Пока слой не отвердел окончательно, самое время проделать и подправить отверстие под горловину топлива. Также на фотографии можно заметить, что волокна стеклопластика расположены под углом 45° по направлению к хорде крыла для получения максимальной прочности.
Две части центрального крыла готовы, а пластиковое покрытие надежно защищает деревянный остов самолета от солнечных лучей.
Лонжерон крыла самолета
Лонжероны – это стыковые узлы крыльев, которые являются частью компенсаторных узлов. Помимо лонжеронов, к компенсаторам также относят подмоторные рампы, различные подвески и прочее. Это продольный основной элемент силового набора самолета. Он выполняет функцию передачи растягивающих, изгибающих, сжимающих и других типов нагрузок. Существует несколько видов лонжеронов – балочные, ферменно-балочные, ферменные, коробчатые. Кроме того, лонжероны принимают участие в восприятии перерезывающей силы. Коробчатого и круглого сечения лонжероны способны воспринимать крутящийся момент.
У летательных аппаратов лонжероны совмещаются со стрингерами и создают продольный набор крыла, оперения, фюзеляжа, элеронов и рулей.
Конструкция
С конструктивной точки зрения лонжероны бывают сборными или монолитными. Сборный лонжерон обладает нижним и верхним поясом и стенкой. Коробчатое сечение имеет только две стенки. Со стенкой пояса соединяются путем клепки, точечной электросварки, болтовых соединений или склейки. Пояса работают от изгибающего момента на растяжение-сжатие. Они составляют большую часть всей площади сечения лонжерона.
Моноблочное крыло – это тип конструкции крыла, у которого при изгибе продольные силы воспринимаются стрингерами и обшивкой по всему поперечному контуру. В таких крыльях лонжеронов нет, но вместо них устанавливаются продольные стенки.
Пояса лонжерона создаются из высококачественных материалов:
- сталь;
- титан;
- алюминиевые сплавы.
При создании формы сечения конструкторы руководствуются определенной задачей – обрести максимальный момент инерции при заданной площади сечения, простотой изготовления, удобством выдерживания профиля, экономии и удобств закрепления к обшивке и стенкам.
По ширине вытянутая форма сечения профиля повышает момент инерции лонжерона. Благодаря присутствию лапок площадь поясов, которая занята отверстиями под заклепки, становится небольшой, а крепление стенки и обшивки к поясу значительно упрощается. Профиль крыла держится за счет малой ковки профилей и их лапок, но в том случае, если это возможно. В других вариациях на пояса устанавливают накладки из мягкого материала.
Применяя профили разного сечения, можно измерить площадь самого сечения поясов в длину. Разрушение пояса при сжатии образовывается от напряжений, равных прочностному пределу материала. При этом пояс работает далеко не всей площадью, а только ее частью, которая равна площади пояса.
Критические напряжения сжатия поясов балочного лонжерона
В двух плоскостях пояс балочного лонжерона подкреплен жесткими элементами – стенкой и обшивкой. Они препятствуют искривлению оси пояса, что приводит к отсутствию потери устойчивости. Критические напряжения определяются так же, как и у стрингеров.
Стенки балочных лонжеронов создают в основном из листовых материалов. Тонкие стенки подкрепляют стойками, как правило, уголкового сечения. Основная задача стойки – разделить стенку на несколько панелей и повысить касательные критические напряжения потери устойчивости, зависящей от соотношения h/a и толщины стенки.
В конструкции лонжерона бывает одна или две стенки. Критические напряжения сдвигания стенок намного меньше, чем толстых. По этой причине одна толстая стенка выгоднее в весовом отношении, чем две тонкие, которые рассчитаны на ту же нагрузку.
КРАТКОЕ ТЕХНИЧЕСКОЕ ОПИСАНИЕ. Истребитель Ла-5 [Сломавший хребет Люфтваффе]
КРАТКОЕ ТЕХНИЧЕСКОЕ ОПИСАНИЕ
Ла-5 — деревянный низкоплан. Основным конструкционным материалом была сосна. Для изготовления полок коробчатых лонжеронов крыла и некоторых шпангоутов использовали дельта-древесину. Деревянные детали планера склеивали смоляным ВИАМ-Б-3 или карбамидным клеем КМ-1.
Крыло — двухлонжеронное, состоящее из центроплана и двух отъемных частей (консолей), набиралось из двояковыпуклых несимметричных профилей NACA-23016 и NACA-23010 относительной толщиной 16 и 10% соответственно и технологически делилось на центроплан и консоли. Между лонжеронами центроплана находились выклеенные из фанеры два кессона для топливных баков.
Консоль крыла
Фюзеляж ЛА-5
Конструкция центроплана самолета ЛА-5
Конструкция руля высоты самолета Ла-5
Конструкция руля поворота самолета Ла-5
Конструкция элерона самолета Ла-5
Конструкция стабилизатора самолета Ла-5
Приборная доска летчика
Капот двигателя
Силовой набор центроплана Ла-5 включает десять нервюр, преимущественно деревянных, за исключением торцевых, изготовленных из металла. Эти нервюры имели трубу, связывавшую оба лонжерона, и проходившую сквозь передний лонжерон. Труба предназначалась для крепления основной опоры шасси. В носовой части центроплана находились выемки — купола, предназначенные для уборки колес шасси. Обшивка крыла между лонжеронами — фанерная, носка — выклеена из шпона.
Силовой каркас каждой консоли помимо лонжеронов включает 15 нервюр ферменного типа, концевого обвода и набора стрингеров. Обшивка консолей крыла между лонжеронами — фанерная, переменной толщины, а носка — выклеена из фанеры. В промежутках между первой и седьмой нервюрами консолей между лонжеронами вклеен кессон под топливные баки.
Консоли крыла имели угол поперечного V=5° по нижней кромке заднего лонжерона. На истребителях Ла-5ФН тип «41» завода №21, начиная с 1944 года, в центроплане и консолях крыла устанавливали металлические лонжероны. К консолям с фанерной обшивкой крепились автоматические предкрылки, щитки-закрылки типа «Шренк» и элероны типа «Фрайз» со 100-процентной весовой и осевой аэродинамической компенсацией. Элероны имеют дюралюминиевый каркас, обшитый перкалью. На левом элероне имелся триммер.
Щитки-закрылки расположены между фюзеляжем и элеронами. В разъеме крыла сделан разъем для щитков. Подвеска — петлевая. Главный профиль, нервюры и обшивка щитка — из дуралюминия. Управление щитками — гидравлическое. В убранном положении щитки-закрылки запираются шариковым замком подъемника.
Сектор газа
Схема питания пушек СШ-20 (ШВАК) самолета ЛаГ-5
Концевые предкрылки выполнены клепаными из дуралюминия. Механизм автоматического открывания предкрылка — коромыслового типа и состоит из двух качалок с ограничителем.
Для сравнения квадратный метр деревянного крыла самолета Ла-5ФН выпуска 1943 года весил 23,8 кг, а у цельнометаллического Bf 109G-2 — 22 кг.
Фюзеляж состоял из металлической передней фермы и деревянного монокока, выполненного за одно целое с килем. Его каркас состоял из четырех лонжеронов и 15 шпангоутов. Фюзеляж наглухо соединен с центропланом крыла четырьмя стальными узлами. Кабина пилота закрыта фонарем, состоявшим из козырька и сдвижной части, стопорящейся в открытом и закрытом положениях. На шпангоуте за кабиной летчика установлена бронеплита толщиной 8,5 мм.
Горизонтальное оперение — свободнонесущее, стабилизатор — двухлонжеронный, цельнодеревянный с фанерной работающей обшивкой. Стабилизатор состоял из двух половин, крепившихся к силовым элементам хвостовой части фюзеляжа. Руль высоты с триммером имел дюралевый каркас, обшитый полотном, и также состоял из двух половин.
Артиллерийский лафет
Шасси — убирающееся трехопорное с хвостовым колесом. Основные опоры имели масляно-пневматические амортизаторы. Основные колеса размером 650×200 мм имели воздушно-камерные тормоза. Хвостовая свободно ориентирующаяся опора, закрепленная на 12-м шпангоуте фюзеляжа, снабжена колесом размером 300×125 мм и убирается в фюзеляжную нишу. Уборка и выпуск шасси и хвостового колеса осуществляется с помощью гидропривода.
Шасси в убранном положении фиксируется с помощью замков, открытие и закрытие которых осуществляется с помощью гидравлики. При аварийном выпуске шасси замки открываются вручную с помощью тросовых тяг. Шасси и костыль в выпущенном положении автоматически запираются жидкостью, заполняющей подъемники и дополнительно: основные опоры — механическим шариковым, а костыль — механическим штыревым замками.
Амортизаторы шасси и костыля — масляно-пневматические. Тормоза колес — воздушно-камерные, дифференциал торможения колес связан с педалями ножного управления.
Управление самолетом — смешанное: элеронами с помощью жестких тяг, рулями высоты и поворота — тросовое. Выпуск и уборка шитков-закрылков осуществлялись с помощью гидропривода.
Силовая установка состояла из звездообразного двигателя воздушного охлаждения М-82А номинальной мощностью на высоте 2050 м 1540 л.с. при 2400 об./мин. (на Ла-5 — М-82Ф, на Ла-5ФН — АШ-82ФН) и трехлопастного винта изменяемого шага ВИШ-105В диаметром 3,1 м с центробежным регулятором оборотов Р-7. Углы установки лопастей винта от 22° (малый шаг) до 51° (большой шаг).
Костыльная опора Ла-5
Выхлопные патрубки соединялись в два коллектора реактивного типа. Для регулировки температуры мотора служили лобовые жалюзи, располагавшиеся в переднем кольце капота и две створки по бокам капота за мотором. Сотовый маслорадиатор — под двигателем, в туннеле нижней створки капота. На выходе туннель имел регулируемую заслонку. Мотор запускался сжатым воздухом. Масляный бак емкостью 59 литров размещался в фюзеляже в месте стыка деревянной части и металлической фермы. Горючее объемом 539 литров (390 кг) находилось в трех центропланных и двух консольных баках (впоследствии центропланные баки для облегчения самолета сняли, сократив общий объем центропланных до 480 литров).
Вооружение состояло из двух синхронных пушек ШВАК (СП-20) калибра 20 мм с общим боекомплектом 340 патронов (иногда самолеты комплектовались 20-миллиметровым орудием и пулеметом калибра 12,7 мм) с пневматическим и механическим перезаряжанием и коллиматорным прицелом ГТБП-la. Орудия размещены на металлической ферме фюзеляжа, доступ к ним осуществляется через откидные верхние крышки капота двигателя. Патроны подаются из двух коробок, закрепленных также на металлической ферме фюзеляжа. Управление оружием — пневматическое. Для стрельбы из пушек на ручке управления самолетом имеется гашетка.
На самолетах Ла-5ФН устанавливали крыльевые бомбодержатели, рассчитанные на подвеску двух бомб калибра 50 кг или 100 кг.
В состав оборудования кроме стандартного набора пилотажно-навигационных и контролирующих приборов, аптечки, входили коротковолновая радиостанция РСИ-4 (радиопередатчик РСИ-ЗМ1 и приемник РСИ-4А), кислородный прибор и посадочная фара. На самолетах Ла-5ФН устанавливались система нейтрального газа, защищавшая топливные баки от возгорания, а также кислородные приборы КПА-3бис или КП-12. Запаса кислорода хватало для полета в течение полутора часов на высоте 8000 м.
НГТУ — ПОДРУЖИН Е.Г. — Самолет По-2
Проектирование, а затем и постройка самолета По-2 были начаты в феврале 2009 года. Инициатором проекта выступила Новосибирская Региональная общественная организация содействия авиации (РООСА). Изготовление рабочих чертежей агрегатов, узлов и их деталей велось по существу заново, поскольку в качестве источников информации сохранились и были использованы технические описания самолета и учебники для летного и технического состава училищ ГВФ (издания 1937-1951 г.г.). Эти описания содержали ряд неточностей, опечаток, был большой дефицит информации по размерам, на ряд узлов и деталей чертежей вообще не было (это относится в частности к бипланной коробке крыльев). Все это приходилось просчитывать и прорисовывать самим, самим же пришлось произвести поверочный расчет коробки крыльев, провести испытания на растяжение-сжатие деревянных клееных полок лонжеронов. Результаты испытаний показали более высокие характеристики (предел прочности) сосновых полок, нежели приводимые в литературе. Это следует отнести к тщательному выбору материала древесины и качеству изготовления полок.
Постепенно, по различным источникам восстанавливались технологии изготовления деревянных узлов и агрегатов. Какие-то технологии адаптировались к современным материалам и оборудованию, а какие-то разрабатывались заново. К работе привлекались студенты старших курсов, впоследствии их усилия трансформировались в дипломные проекты и ВКРБ.
В настоящее время собраны бипланная коробка крыльев с носовой частью фюзеляжа и заканчивается сборка хвостовой балки с Г.О. и В.О. Начат монтаж системы управления самолетом.
С благодарностью примем любую информацию по документации на самолет, об агрегатах и узлах планера, сохранившихся в любом сотоянии.
11 июля 2015 года самолет По-2 совершил первый полет (аэродром Мочище, 3 часа пополудни).
Wooden It Be Lovely? — Часть вторая: Создание крыльев
Какая часть является наиболее важной, незаменимой частью любого самолета? Крылья, конечно. Были и бесхвостые конструкции, и летающие крылья без фюзеляжей, и планеры без двигателей, но на самом деле нет самолета без крыла.
Учитывая центральную важность крыла для любого самолета, почему я должен сначала построить крыло?
Что ж, в моем случае это была комбинация промедления — я мог отложить принятие определенных решений по конструкции фюзеляжа — и представления о том, что создание крыльев с их нервюрами и лонжеронами представляло меньшую проблему для моего строительства. способности.Не поймите меня неправильно; На самом деле крылья представляют собой гораздо больше сборочных работ, чем фюзеляж или хвостовая часть Pietenpol. Сначала необходимо изготовить зажимное приспособление нервюры, затем построить 32 нервюры, затем установить нервюры на лонжероны, затем прикрепить переднюю и заднюю кромки, а затем — различные стойки сжатия, а также тросы сопротивления и сопротивления. Затем, конечно, элероны должны быть установлены на место и вырезаны из конструкции крыла.
Готовимся
До того, как был разрезан первый кусок шпильки или изготовлен приспособление для ребер, первым делом, как предложил один мудрый человек из списка Пиетенполя, было тщательно изучить планы. Я получил планы примерно за месяц до прибытия дров, так что у меня было время внимательно их рассмотреть и начать выяснять порядок, в котором все должно быть сделано. Я также начал составлять список инструментов, которых мне не хватало и которые мне понадобились, и второй список оборудования и расходных материалов, которые нужно было заказать.
Air Camper, в отличие от многих других проектов домостроения, недоступен в виде комплекта. Есть поставщики комплектов материалов, такие как Western Aircraft Supply и Aircraft Spruce and Specialty, а также поставщики компонентов, такие как Replicraft.Но Pietenpol — это то, что называют проектом, построенным по плану. Вы покупаете планы из одного источника, а материалы для его строительства получаете из других источников.
Немного истории о Pietenpol Air Camper и Бернарде Питенполе, насколько я знаю. Насколько я понимаю, в оригинальном Air Camper использовались ель и пихта, которые Берни Питенпол получил от местного поставщика пиломатериалов.

К тому времени, когда моя ель прибыла на флигель в конце ноября 1999 года, я изучал планы больше месяца. Меня беспокоило одно — отсутствие у меня опыта в металлообработке, особенно в сварке.Решил купить стальную арматуру для сборки крыла в Replicraft. Replicraft поставляет большую часть стальных компонентов, необходимых для Pietenpol, а также собранные нервюры и фюзеляжи. Я заказал крепежные ремни крыла, крепежные элементы ремня крыла центральной секции / кабана, внутренние шкивы элеронов, кронштейны крепления летучей стойки, фитинги крепления троса сопротивления / сопротивления и рупоры управления элеронами. Все они были изготовлены из стали 4130, подвергнутой лазерной резке, при необходимости сварены TIG и загрунтованы хроматом цинка.Стоимость стальной арматуры составила 510,10 долларов.
Получив ответ на вопрос о стальных частях, по крайней мере, для крыла, и планы, которые теперь были подорваны всем вниманием, которое они получали, я был готов начать строительство нервюр, как только прибыла древесина.
Для начала нам понадобится приспособление…
Первым заказом после инвентаризации партии ели было изготовление зажимного приспособления нервюр крыла. В основном это форма, выложенная на тяжелую основу из фанеры или другого твердого, неискаженного материала.На основании точно нанесены внешние размеры, верх и низ ребра, а затем к основанию прикрепляются блоки, которые удерживают верхние и нижние ограничители и внутренние распорки на месте для склеивания. Короткие куски лонжерона также прикрепляются к основанию в правильном месте, чтобы гарантировать, что готовые нервюры будут скользить по лонжеронам и правильно сидеть. Я использовал фанеру толщиной три четверти дюйма в качестве основы моего зажимного приспособления. Основание приспособления было размером примерно шесть футов на 18 дюймов, что более чем достаточно для размещения 60-дюймовой хорды ребер.Планы поставляются с фотокопией полноразмерного шаблона ребра, но мои размеры шаблона по сравнению с размерами, указанными на планах, не совпали. Шаблон был примерно на дюйм длиннее, чем требовалось в плане, и расстояния от контрольной линии вдоль хорды выступа до определенных точек вдоль верха и низа выступа также не совпадали. Позже я узнал, что бумага, на которой копируется шаблон, часто немного растягивается в процессе копирования. Я начал с нуля и измерил и повторно измерил точки, которые определяют верхнюю и нижнюю поверхность выступа, как указано на планах.Затем я аккуратно нарисовал линии, соединяющие точки на базе кондуктора. Эти линии будут определять форму аэродинамического профиля крыла, и я проверил и перепроверил эти измерения, чтобы убедиться, что я правильно их понял.
Убедившись, что мой контур ребра в порядке, я вырезал несколько десятков блоков размером один дюйм на дюйм из оставшейся фанеры, склеил и прибил их так, чтобы внутренние края блоков лежали как раз на контуре контура ребра. . Затем я приклеил и прибил блоки к внутренней части лески, смещая блоки на четверть дюйма плюс часть, чтобы оставалось достаточно места для прохождения еловой полоски между внутренним и внешним блоками. Этот зажим фиксирует верхние и нижние еловые полосы на месте, и, если распорка установлена правильно, гарантирует, что все ребра будут однородными и что изгибы аэродинамического профиля соответствуют планам.
В дополнение к блокам, которые позиционируют верхнюю и нижнюю планки, я отметил места для внутренних распорок, составляющих ферменную структуру выступа. Я не устанавливал блоки для размещения этих частей, полагая, что смогу разместить их в нужном месте, следуя контурам, отмеченным на основании приспособления.Оглядываясь назад, мне жаль, что я не вставил несколько блоков, потому что мои распорки фермы не получились точно однородными при сравнении одного ребра с другим. Крепление прочное и правильно расположено для обеспечения прочности, и это самое важное соображение. С чисто эстетической точки зрения, совершенно одинаковые ребра были бы неплохими, но они все равно будут закрыты тканью. Тем не менее, по мере того, как я совершенствуюсь с Pietenpol, я усвоил один урок: детали, которые хорошо выглядят и единообразны, лучше подходят друг к другу и, вероятно, приводят к лучшей работе, поэтому теперь я уделяю деталям даже больше внимания, чем когда начинал.
… сделать ребра
Теперь, когда приспособление было построено, пришло время приступить к изготовлению ребер. Я где-то читал, что наращивание ребер происходит намного быстрее, если вы измеряете различные части, из которых состоит ребро, и предварительно нарезаете достаточно частей, чтобы образовать многие или даже все ребра. Поместите отдельные кусочки в мусорные ведра, а затем просто возьмите по одной, чтобы собрать ребро. Таким образом, после того, как разрезание отдельных частей будет завершено, вам не придется постоянно приближаться к пиле каждый раз, когда вы начинаете строить ребро.Я взял немного фанеры, сделал несколько отверстий для ребер и вырезал их примерно на дюжину ребер. Затем мне нужно было придумать способ пропарить или пропитать мои верхние стропы, чтобы они не растрескались и не раскололись, когда они сгибаются, образуя поверхность аэродинамического профиля в зажимном приспособлении. Это было особенно важно от передней кромки до середины хорды из-за большей кривизны верхней передней кромки крыла. Я попросил местный цех металла приварить стальную пластину диаметром 12 дюймов к концу стальной трубы три на 18 дюймов, закрыв конец и сформировав основу.Трубу наполнили водой примерно на две трети, и все это поместили на походную печь на пропане. Я опускаю в трубу несколько полосок, и печь нагревает воду и размягчает дрова. После того, как полоски приготовились какое-то время, по крайней мере, полчаса, я поместил их в простое приспособление, сделанное из куска доски размером два на десять, вырезанного с изгибом, немного превышающим переднюю кромку крыла. После того, как полосы были зажаты в зажимном приспособлении на ночь, полосы высохли с установленным в них изгибом, и при установке в зажимное приспособление для ребер было очень небольшое натяжение.Идея этого возникла прямо из потрясающей книги Тони Бингелиса «Методы строительства спортивных самолетов». Квартет руководств Бингелиса по сборке самолетов необходим любому строителю.
После того, как верхняя и нижняя зажимы были помещены в зажимное приспособление, я пошел к своим голубятням и получил распорки фермы для каждого места. Для этого требовался скос, чтобы он соответствовал верхней и нижней планкам, и я использовал настольную дисковую шлифовальную машину для придания формы каждому стыку. Для каждого соединения требуется косынка или элемент жесткости из авиационной фанеры шириной 16 дюймов.Я вырезал на своей настольной пиле полоски толщиной в один и полтора дюйма из фанерного листа, а затем с помощью пары универсальных резаков вырезал прямоугольные косынки из полос. Некоторым соединениям требовался меньший размер в один дюйм, другим требовалось полторы дюйма, а некоторым требовались треугольные косынки, вырезанные из полуторадюймовой заготовки. Как только подтяжки были сформированы и косынки вырезаны, пришло время приклеивать.
Я использовал эпоксидный клей Т-88, который смешивается один в один. Т-88 довольно терпим к температуре, и он срабатывает даже в холодную погоду, что бывает после того, как я выключу пропановый обогреватель.В холодную погоду эпоксидной смоле требуется больше времени для достижения полной прочности, но она даже полностью затвердевает. Просто в холодную погоду нужно оставлять стыки зажатыми дольше. T-88 также не требует сильного зажима и точной посадки, как некоторые другие клеи. Фактически, вы можете чрезмерно зажать оголенные материалы, такие как T-88, и «заморозить» соединение, выдавив слишком много клея.
Сначала я нанес клей на концы каждой распорки фермы, а затем, после того, как они были установлены, нанес клей на область вокруг стыка, отступив примерно на дюйм, и уложил косынки на место.Затем я прибил полудюймовые авиационные гвозди через косынку к ели, обычно по одному гвоздю на каждую ногу соединения. Он действует как зажим, надежно удерживая косынку и соединение на месте, пока клей застывает. Некоторые пуристы возвращаются после этого и вырывают гвозди в интересах снижения веса. Я оставил гвозди, хотя ценю, что для снижения веса вы должны заботиться о каждом грамме, который попадает в планер.
После того, как косынки были прибиты, я снял ребро с приспособления, приклеил и прибил косынки к другой стороне ребра. Когда ребро было сделано, я повесил его на стержень, прикрепленный к стропилам магазина. В конце концов, у меня была целая коллекция. К тому времени, как я построил несколько, моя техника была лучше, и нервюры были более однородными. Однако внешние размеры и площадь, через которую проходят лонжероны, были идентичны для каждого нервюра, от первого до последнего.
Я дошел до того, что смог закончить ребро примерно за два часа, и я поставил себе целью каждую ночь поработать в магазине. В результате у меня были построены все ребра чуть более чем за месяц.
Затем собрать нервюры на лонжеронах
После обработки нервюр мне понадобился подходящий стол для сборки крыла. Я взял два листа фанеры три четверти дюйма, несколько листов два на четыре и четыре на четыре, и построил стол шириной четыре фута и длиной 13 футов. Я установил на столешницу шайбу, чтобы сделать ее настолько плоской и ровной, насколько это было возможно с помощью уровня.
Затем я взял передний и задний лонжероны и скосил концы и внутренние концы по плану. Затем я взял свою ленточную линейку и измерил центральные точки каждого из нервюр на лонжеронах.После маркировки внешние нервюры были сдвинуты на место, фанерные пластины были приклеены по обеим сторонам лонжеронов, где идут кронштейны подвижных стоек. После нанесения клея я отметил места и просверлил отверстия для болтов, которые проходят через кронштейны подвесной стойки, фанеру и лонжероны. Установка авиационных болтов завершила работу. Затем внутренние нервюры можно было сдвинуть с торца крыла.
Наконец, были вырезаны небольшие клинья для прокладки верхней части нервюр, которые изгибаются, чтобы заполнить зазор между верхней полоской нервюр и верхней частью лонжеронов.Нанесение Т-88 на верхнюю и нижнюю части нервюры приклеило нервюры к лонжеронам, а два авиационных гвоздя толщиной в один дюйм, вбитые в лонжерон нервюры, удерживали все на месте, пока клей не затвердел.
После того, как нервюры были на месте, я установил стальные крепежные ремни крыла на торце панели крыла. Затем были вырезаны и приклеены компрессионные стойки, которые не дают лонжеронам стягиваться друг с другом, одна пара на летучей стойке и одна пара на торце.
Законцовка крыла, которая начинается с куска ели размером один дюйм на один дюйм на 60 дюймов, должна быть изогнута, чтобы приблизительно соответствовать изгибу средней линии аэродинамического профиля.Для этого потребовалось несколько ванн в пароварке, на которую надвинули кусок дренажной трубы из ПВХ с крышкой, чтобы тепло и пар циркулировали вокруг этой пятифутовой еловой палки. Специальное приспособление для сгибания законцовки крыла помогало получить необходимую кривую, и древесина гнулась без раскалывания. Позже я разговаривал со строителем, который ламинировал кончики крыльев тонкими полосками ели, приклеенными приспособлением до толщины в один дюйм. Не знаю, какой метод работает лучше всего, но его звучание звучало очень элегантно.
Так как кончик крыла запотевал, я установил кронштейны тросов сопротивления и троса. Эти перекрещенные проволоки предотвращают отклонение крыла вперед и назад из-за сопротивления в полете. В планах был жесткий провод 14-го калибра. Я заменил стальную проволоку для ограждения 11-го калибра, которую купил в местном магазине. Рукава «Никопресс» закреплены на них с помощью талрепов для регулировки натяжения. Мой технический советник EAA объявил, что проволока для забора полностью подходит для Pietenpol, даже если это вызвало недоумение у другого строителя Piet, с которым я разговаривал. Я полагал, что Берни одобрит.
Позже, после того как были закончены внешние панели, я забеспокоился о проволоке из мягкой стали для забора, вырезал ее и заменил на 1/8-дюймовый кабель из нержавеющей стали 7X19. Я думаю, что проволока для забора подойдет, но я решил, что обратная сторона слишком велика. При замене тормозных проводов я занялся практикой, с которой хорошо знакомы все домостроители, — переделал части, которые вы испортили или сомневаетесь.
Добавить переднюю и заднюю кромки…
Передняя кромка представляет собой кусок ели длиной 13 футов по очереди. Он должен иметь форму параболической передней кромки, и я решил использовать свою настольную пилу для грубой резки углов, под которыми передняя кромка соприкасается с верхней и нижней частью ребер. Это значительно сократило количество операций по строганию. Прижав переднюю кромку к выступам ребер, я просверлил отверстия для маленьких болтов, которые крепят переднюю кромку к ребрам. Затем приклеил и прикрутил переднюю кромку к носикам нервюр. После набора клея я использовал инструмент Stanley Sur-Form, чтобы придать правильную округлую форму передней кромке.Я сделал простую форму из куска фанеры и использовал ее, чтобы убедиться, что форма передней передней кромки соответствует длине крыла.
Задние кромки поставляются Western Aircraft Supply, уже обрезанные до нужной формы. Они были прикреплены с помощью вставок из фанеры диаметром 16 дюймов и приклеены к хвостовикам нервюр.
После того, как панель крыла была по существу построена, я протрубил крыло, что означает, что я проверил, что оно квадратное, измерив диагональ от основания до кончика. Регулируя натяжение тросов с помощью стяжных муфт, я скорректировал разницу в диагонали примерно на полдюйма. Затем стяжные муфты были закреплены предохранительной проволокой, чтобы они не проворачивались.
… и элероны и вещи
Элероны устанавливаются на место, чтобы гарантировать правильную посадку элеронов. Фальшивый лонжерон, который обрамляет отверстие элеронов в крыле, и передняя кромка элеронов требуют точной резки под углом на настольной пиле.Это определенно был случай «дважды отмерь и один раз отрежь», но обе части вышли нормально. Другой кусок ели образует лонжерон элеронов. Эти детали вставляются в ребра и приклеиваются. С добавлением некоторых внутренних распорок элерон был готов, хотя он все еще оставался частью крыла.
Затем пришло время изготовить три шарнира элеронов. Они начинаются как стандартные трехдюймовые петли для ремешка, которые сгибаются до нужной формы. Несъемный шарнирный штифт выдвигается, и съемные штифты авиационного класса образуют шарнирные штифты. Я приварил отверстия для винтов и петли петель, чтобы образовать замкнутый круг, укрепив петли. Затем на сверлильном станке просверливали новые крепежные отверстия.
Как только шарниры были прикручены болтами, я вытащил штифты шарниров и выпилил элероны из крыла, разрезав ребра там, где находится зазор элеронов. Удивительно, но когда штифты вошли обратно, элероны работали без заедания. Я беспокоился об использовании петель из хозяйственного магазина, но, посмотрев на готовый продукт и сравнив их с петлями элеронов на серийных самолетах, я не беспокоился.Петли Piet выглядят намного прочнее и мощнее.
Нужно было установить еще несколько распорок и сделать кронштейн внешнего шкива элеронов, но на этом, по сути, закончилась панель крыла. Последней задачей было покрыть всю древесину двумя слоями эпоксидного лака, следя за тем, чтобы нанести лак на все укромные уголки и трещины, например, за косынками ребер и внутри соединительных швов. После высыхания я повесил готовую панель крыла на стропила и приступил к работе со второй панелью.
Затем проделайте все еще раз для другого крыла
Включая все нервюры, мне потребовалось восемь месяцев, чтобы закончить панель левого крыла. На правое крыло ушло около четырех месяцев. Центроплану крыла потребовалось еще три месяца, в основном потому, что я внес некоторые изменения в планы, в том числе переместил топливный бак из центральной секции в фюзеляж и вырезал полукруглую область на задней кромке центроплана, чтобы легче садиться и выходить из задней кабины.
Люди, которые заходят проверить мои успехи, отмечают, что крыло Pietenpol действительно сочетается друг с другом, как большая модель из пробкового дерева, и они правы. Большая часть конструкции, от наростов нервюр до двойных еловых лонжеронов, выглядит как увеличенная модель. В юности я построил несколько летающих или вроде как летающих моделей. Судя по показателям некоторых из этих моделей, я не уверен, что эта мысль заставляет меня чувствовать себя комфортно или нервничать. Зная, что моя задняя часть будет летать на этой большой модели, я стал намного более внимательным, чем я мог бы быть с бальзовыми и тканевыми моделями 30 лет назад.
Далее — фюзеляж…
Изготовление конических ребер
В выпуске KITPLANES за октябрь 2007 г., в статье, озаглавленной «O для некоторых планов!» Я описал свою начальную работу по восстановлению пилотажного самолета Dalotel DM165. С тех пор я приобрел весь набор планов дизайнера Мишеля Далотеля и добился значительных успехов в его восстановлении, хотя мне еще предстоит пройти долгий путь. Одна из наиболее сложных задач, стоящих передо мной, которая может встать перед любым строителем с подобными конусообразными крыльями, заключалась в изготовлении различных нервюр крыла.В Dalotel каждое крыло имеет 14 ребер, и они разные с каждой стороны, поэтому имеется 28 уникальных ребер. Это одна из причин такой популярности так называемых крыльев Hershey-bar с ребрами только одного размера. Вы делаете одну приспособление и вытаскиваете все необходимые ребра.
Единственный Dalotel DM165, совершавший полет над Францией примерно в 1969 году. Самолет был полностью пилотажным.
Далотель попал в аварию до того, как я его купил, и оба крыла были сильно повреждены. Крылья деревянные, с двумя деревянными лонжеронами. Крыло обшивается фанерой, которая затем обшивается тканью.Левое крыло было в лучшей форме, чем правое, и с этого я начал. Сначала мне пришлось снять весь укрывной материал, чтобы увидеть, что было разрушено и что, возможно, можно было спасти. Это удаление было достаточно сложным, чтобы потребовать еще одну статью, но не сейчас, спасибо.
Один из чертежей, по которым был построен оригинальный самолет. Это для ребра номер восемь. В таблице внизу указаны смещения для внешнего контура. Все размеры являются метрическими, а примечания — на французском языке.Автор искренне благодарит за существование Google Translate.
Я обнаружил, что левый главный лонжерон в приличной форме. Задний лонжерон и большая часть нервюр были повреждены в результате вынужденной посадки. Я снял все обшивки и аккуратно снял все нервюры с лонжерона, спасая что мог. Лонжерону нужно было снять и заменить только одну из его накладок, и тогда все было в порядке. Так что оставалось отремонтировать несколько нервюр и изготовить остальные, включая полный комплект для другого, гораздо более поврежденного крыла.
Плинтус, на котором собраны все 28 ребер. Контур ребра нанесен на плинтус со смещениями. Полоса крышки фиксируется на месте, совпадая с изгибом на плате, сгибая ее и удерживая изгиб с помощью нескольких блоков, прикрепленных к доске штифтами 18-го калибра. Это быстро и легко, и как только ребро будет построено, блоки и плинтус можно будет использовать повторно. Для этой техники требуется булавочный пистолет, воздушный компрессор и булавки правильной длины, чтобы не пригвоздить плинтус к скамейке.Пригодится и пневматический степлер.
Это ребро готово к выходу из зажимного приспособления. Все клеевые соединения затвердели, и были добавлены скобы из фанеры толщиной 1/16 дюйма. Подтяжки из фанеры были оставлены большими для последующей обрезки.
Наконец, планы
После двух лет борьбы с самолетом я получил подарок от французского летчика-испытателя Кристофа Маршана в виде компакт-диска со всеми оригинальными чертежами Dalotel, включая все рисунки нервюр. Каждый чертеж ребра имел детали его контура в виде таблицы смещений.На чертежах ребер также показано размещение распорок, изготовленных из фанеры толщиной 1/16 дюйма, которые не покрывают все ребро. Чтобы получить форму и размер каждой нервюры, вы находите плоскую поверхность и рисуете контрольную линию, которая в основном является хордой крыла. Затем, начиная с переднего края, который равен нулю на диаграмме, вы измеряете заданное расстояние от диаграммы вдоль базовой линии и отмечаете эту точку. Наконец, вы измеряете вверх и вниз от этой продольной точки в соответствии с размерами «y» вверх и вниз, указанными на схеме ребер, и отмечаете эти места точкой.
Продолжая этот процесс для всех значений смещения, указанных в таблице, вы получите серию точек, которые, если вы все сделали правильно, попадут на контур выступа. Соедините точки плавной кривой, и на вашем выкройке появится контур ребер в полный размер. После того, как у вас будет контур ребра, следующим шагом будет добавление блоков к плинтусу, чтобы полоски заглушек были изогнуты по форме, и дополнительных блоков, чтобы разместить вертикальные соединяющиеся части ребра на месте, а затем склеить их все вместе.
Ребро рождается. К ребру, только что вынутому из джига, добавлены дополнительные детали. Кусочки вощеной бумаги легко снимаются. О раскладке фанеры внахлест позаботится окантовочный фрезер.
Можно было бы ожидать, что для каждого ребра придется изготовить зажимную форму или форму ребра. Это означает, что в случае с Dalotel у меня было бы 14 рисунков ребер на 14 больших кусках фанеры, приспособления для которых почти наверняка никогда не будут использоваться снова. Кроме того, фанера, удерживающая 14 форм или форм, обычно была бы бесполезной, поскольку все блоки приклеены к ней для придания формы полосам крышки и позиционирования соединительных элементов. Однако для меня это было совершенно не так. Я придумал систему, с помощью которой было настолько легко построить мои ребра, что я подумал, что было бы неплохо поделиться ею с сообществом домостроителей в надежде, что это может побудить других строить конические крылья.
Лучший способ сделать ребра
Я начал с самого большого ребра, номер один. Это почти шесть футов в длину и около десяти дюймов в высоту. Мне нужен был кусок фанеры несколько длиннее и выше этих размеров, чтобы дать место для всех блоков, которые я собирался прикрепить к доске, чтобы удерживать детали на месте, пока клей — в моем случае эпоксидная смола West System — застывал.Для плинтуса я использовал кусок фанеры толщиной в полдюйма. В моем магазине я мог легко поддерживать этот относительно тонкий фанерный плинтус, чтобы он оставался совершенно плоским, пока я строил ребра. При необходимости можно укрепить плинтус с помощью перпендикулярных распорок или ферм за ним или использовать более толстую фанеру.
Роутер в работе. На конце фрезы есть шарикоподшипник, который упирается в полосу крышки. Результат — идеально обрезанные края за секунды.
Новое ребро показано рядом с оригиналом, нос которого сломали при жесткой посадке.Автор собирается положить накладки на верхнюю часть нового выступа по образцу оригинала и внимательно посмотреть на рисунок выступа на планах. Были некоторые расхождения между рисунками и реальными ребрами жесткости. В таких случаях автор подбирал существующее ребро, а не план. Обратите внимание на отверстия в оригинале, которых не будет в новом ребре. Они предназначались для контрольных проводов системы спойлеров, которая не работала и была заблокирована первоначальным производителем. Восстановленный самолет не будет иметь спойлеров.
Вот еще одно ребро, которое вот-вот будет прикреплено «другой стороной», рядом с серым оригиналом. Носовой блок на многих нервюрах сделан из бальзы, зажатой между ребрами жесткости из фанеры красного дерева толщиной 1/16 дюйма. Распорки находились на противоположных сторонах нервюры на правом и левом крыле.
Затем я провел по дереву хорду или контрольную линию. Это послужило основой для всех размеров каждого ребра будет построен, и да, я только что один кусок подложки фанеры для всех 28 ребер.Разница между правым и левым ребрами жесткости заключается в размере и размещении всех 1/16-дюймовых раскосов из фанеры, косынок и панелей, приклеенных по бокам каждого ребра. Некоторые были большими, некоторые маленькими, и единственное отличие от левого крыла к правому заключалось в том, что большие и маленькие части были на противоположных сторонах. Когда я построил каждое ребро, я положил соответствующие распорки на верхнюю сторону, пока ребро было в приспособлении; Когда ребро затвердело, я снял его с зажимного приспособления и наложил соответствующие скобы с другой стороны ребра. Для второй стороны кондуктор мне не понадобился, потому что форма ребра была задана и полностью закреплена еще до того, как оно вышло из приспособления.
С опорой или базовой линией посередине моего базового фанерного приспособления я перешел к чертежу ребра номер один и расположил смещения, измеряя их вверх и вниз от базовой линии, и нарисовал маленький кружок вокруг каждой точки. Все рисунки ребер напоминали рисунок ребра номер восемь (см. Фото). Расстояние вдоль хорды указывается как в процентах от хорды, так и в размерах «x», начиная с x = 0 на передней кромке. Размеры «y» идут вверх и вниз от этого линейного расстояния вдоль базовой линии.Все размеры на всех чертежах этого самолета указаны в метрических единицах. Самый простой способ обойти это — купить выдвижные метрические весы, которые делает Стэнли (Stanley 5M, 30-497). Или вы можете преобразовать размеры — и рискуете ошибиться.
Теперь, когда у меня есть серия точек, обозначающих изгиб, я использовал полоску крышки в качестве французской кривой, согнул ее вдоль точек и нарисовал соединительную линию, чтобы показать контур выступа на плинтусе. Хотя не было необходимости соединять точки, я увидел контур ребра, чтобы упростить регулировку, когда я согнул верхнюю и нижнюю полоски крышки и зафиксировал их на месте. Я также обратил расположение соединительных стоек на подложку деревянной планки, вырезать их, чтобы соответствовать точно между верхней и нижней полос крышки, и запер их в месте с большим количеством блоков. Я использовал карандаш для всех отметок, так что я мог стирать по мере необходимости в процессе.
Центральным элементом является булавочный стрелок 18-го калибра, удерживающий все блоки на месте. Два других являются скобозаборниками для крепления накладок к планкам заглушек. Почему два? Вам не нужно искать подходящие скобы и возиться с порядком перезарядки, когда в одном пистолете заканчиваются скобы и эпоксидная смола быстро схватывается.
Добавление деревянных блоков
Я заранее подготовил связку деревянных блоков. Они были примерно 1 дюйм на 11/8 дюйма и толщиной 3/8 дюйма. Я хотел, чтобы блоки были ниже уровня полосок крышки, которые на моих ребрах имеют ширину 1/2 дюйма и толщину 1/4 дюйма. Ребро номер один было толще, но идею вы поняли. Я поместил эти блоки на опорную пластину внутри и снаружи полосы крышки таким образом, чтобы заставить гибкую полосу крышки соответствовать правильному контуру выступа. Как только полоса крышки совпала с контуром ребра, я выстрелил булавкой 18-го калибра из пневматического пистолета для гвоздей через блоки, которые удерживали ее на месте.Некоторые блоки занимали по два штифта. Вертикальные соединительные элементы выступа также были размещены с блоками, прикрепленными таким же образом.
После того, как верхняя и нижняя полоски крышки и соединительные элементы были на своих местах, а передний соединительный деревянный блок был расположен аналогичным образом, я поднял каждое соединение дерева с деревом и положил под него небольшой кусочек вощеной бумаги, чтобы узел не прилипал. на плинтус, когда эпоксидная смола застынет. Затем, тщательно отмерив эпоксидную смолу, склеив и перемешав, я приклеил каждый кусок на место.На этом этапе не было ни одного гвоздя через полоски крышки, а было просто множество маленьких блоков, удерживающих все на месте. За исключением времени отверждения, которое я установил на 24 часа, эта процедура заняла всего несколько минут, а не дней, чтобы сделать постоянную приспособление для каждого ребра.
Этот пневматический пистолет стреляет скобами через обрезки древесины, затем через закрывающие скобы и в полосу крышки. Это отличный способ сделать герметичные эпоксидные швы.
Скобы маленькие, чтобы не расщепить полоски елового колпачка.Вот их стопка рядом с карандашом.
Вот как скобы удерживали большой лист фанеры, закрывающий стабилизатор самолета. Это стандартная технология строительства самолета из дерева.
На следующий день, когда ребро все еще было в зажимном приспособлении, я добавил скобы из фанеры толщиной 1/16 дюйма. Установочные блоки находились ниже уровня выступа, поэтому они не мешали крепежным пластинам размером 1/16 дюйма. Соблюдая направление волокон, я обрезал их до нужной ширины, но позволил им выступать за верхнюю и нижнюю полоски крышки, чтобы они были обрезаны позже.Таким образом, не было утомительного формования и борьбы за то, чтобы поставить их в нужное место.
Вот почему вы используете древесные отходы вместо хороших материалов, чтобы скрепить их вместе. Удаление скоб с помощью заточенной отвертки и больших плоскогубцев обычно приводит к разрушению полос, но важная древесина под ними не повреждается ни в малейшей степени.
Неповрежденная хорошая древесина показана рядом с существенно разрушенными элементами защитного покрытия. Когда фанерная распорка должным образом прикреплена к планкам крышки, все, что нужно, — это несколько секунд с маршрутизатором, чтобы подготовить ребро для раскосов с другой стороны.
Удалите старые блоки и приготовьтесь выложить следующее ребро на единственном плинтусе, используемом для всех 28 ребер — дело нескольких минут. Большинство блоков можно использовать повторно, просто протянув через них штифты.
Есть несколько способов закрепить их по мере отверждения эпоксидной смолы. Один из них — добавить вес, но при этом скоба может сместиться. Лучший и более управляемый способ — использовать точно установленные скобки от пневматического степлера, выстреливаемого через фанерную распорную пластину в нижележащую еловую заготовку. Я никогда не прикрепляю скобу непосредственно к приклеиваемой детали по нескольким причинам. Я использовал полоску фанеры или ели вдоль линии скрепления накладки. Скобы протыкались через металлолом, затем через хорошую фанеру, а затем в полоску крышки под ней. Это позволило легко удалить скобы после того, как эпоксидная смола затвердела, не повредив хорошую древесину тонкой пластины жесткости, и конюшни не приклеиваются к хорошей древесине. Скобы были тонкими, чтобы не раскалывать ель. Когда они застыли, я вытащил скобы с помощью заточенной отвертки и плоскогубцев и снял ребро с приспособления.
Это первое ребро, построенное на плинтусе, номер один. Он толще и тяжелее по всем своим размерам и требует немного иной техники, чем все остальные, но он подтвердил концепцию использования одной доски, пневматического гвоздезабивателя и степлера, а также изобретательность, позволившую упростить создание конических ребер.
Обрезка
Затем я смог обрезать перекрывающиеся усиливающие пластины небольшим фрезером, используя кромочную фрезу на шарикоподшипниках. Шариковый подшипник упирается в полоску крышки, а резак удаляет всю перекрывающуюся фанеру.Это было быстро, очень точно и работало как чемпион. Затем я мог бы добавить необходимые закрывающие полосы к другой стороне нервюры, использовать мое приспособление для изготовления второго выступа для другого крыла, а затем перейти к следующей паре.
Для подготовки плиты основания для следующего набора ребер, это было делом нескольких минут, чтобы просто вытащить все блоки с моей опорной плитой с помощью молотка. Я мог повторно использовать блоки один или два раза, протягивая штифты через блок. Каждая пара нервюр была меньше, чем предыдущая пара, поэтому следы было легче увидеть, а опорная древесина была по существу свежей и неиспользованной.Как уже отмечалось, я разложил позиции карандашом и мог легко стереть свои отметки, если они помешали следующей настройке.
Это был чрезвычайно эффективный и простой способ изготовления конических ребер. Теперь у меня есть все ребра, необходимые для этого грандиозного реставрационного проекта. Один комплект уже стоит на отремонтированных лонжеронах левого крыла. Мне все еще нужно сделать лонжероны для подходящего, но, похоже, это не такая уж большая работа, потому что я дополнил все, как он построен. Я полностью разделил старый главный лонжерон пополам, чтобы увидеть, что было внутри, и теперь, когда у меня есть планы, я могу точно видеть, как я собираюсь это делать.Прямо сейчас я занимаюсь разработкой новой установки для убирающегося шасси и изготовлением деталей для зубчатого механизма. Шасси ставило меня в тупик более трех лет, потому что оригинальные колеса и шины больше не были доступны. Теперь, благодаря продуктам Beringer Aero и небольшому изменению дизайна, я вижу свет в конце этого туннеля.
Это набор из 14 нервюр для правого крыла, которому нужны пара лонжеронов, некоторые хитрые воздухозаборники, покрытие и еще одна или две маленькие детали.
Spars-The Heart of the Wing
Я встретил свой первый лонжерон крыла, когда мне было 13 лет. Я присоединился к группе мальчиков, которые собирались в FBO, чтобы восстановить пару J-3 Cubs — владелец FBO получил бесплатную рабочую силу, а мы получили образование, которое в конечном итоге включало уроки полета, что было беспроигрышным для всех. В ту первую ночь мне вручили кисть и банку лакового лака и велели покрыть эту длинную деревянную плиту. Это было сердце крыла J-3, которым мы в конечном итоге должны были летать. На мой взгляд, это было похоже на длинную доску, но мне сказали, что это дерево особого сорта, ситкинская ель, известная своей длинной, прямой и однородной текстурой.Мне это показалось симпатичным, но потребовалось еще много лет, чтобы построить самолеты и учиться на авиационного инженера, чтобы действительно понять, насколько особенным на самом деле является главный лонжерон крыла. Это больше, чем просто место для крепления ребер — это ядро конструкции, поддерживающей полет.
Мы собираемся начать эту серию из трех частей, посвященных лонжеронам, с обсуждения нагрузок, переносимых лонжеронами, их конструкции и способов использования различных материалов для изготовления различных типов лонжеронов.В следующих статьях мы рассмотрим конструкцию лонжеронов типичного цельнометаллического крыла — в данном случае основные лонжероны для мотоплана Xenos, хороший пример типичного металлического лонжерона с множеством различных компонентов, работающих вместе, чтобы сформировать единое целое. Блок. Мы покажем, как соединяется лонжерон и как различные компоненты работают вместе, чтобы выдерживать полетные нагрузки на длинных тонких крыльях планера. Эти статьи должны дать вам понимание, необходимое для принятия решения о том, хотите ли вы строить собственные лонжероны или покупать их в собранном виде, что сегодня является обычным вариантом для комплектных самолетов.
Одна из заглушек лонжерона для мотоплана Xenos. Обратите внимание на Т-образную форму — вертикальная часть сопрягается с лонжероном, а прочность находится в пределах вершины буквы «Т».
Изгибающие оси
Большинство крыльев, по которым вы встретите, имеют один главный лонжерон, а также задний лонжерон меньшего размера. Эти два элемента действуют вместе, вместе с нервюрами и стойками, чтобы создать жесткий, прочный, но легкий космический каркас, который поддерживает самолет в полете. Главный лонжерон сопротивляется изгибу в первую очередь в направлении вектора подъемной силы, то есть вверх и вниз. В сочетании с остальной конструкцией крыла он противостоит силам в продольном и продольном направлениях, но сам по себе лонжерон на этой оси немного слабоват. Типичный лонжерон выше, чем ширина, и причина этого в том, что основная ось изгиба заключается в том, что крыло в первую очередь хочет изгибаться в направлении вверх и вниз, и, следовательно, оно должно быть толще в этом измерении.
Если вы возьмете кусок пиломатериала размером 1 × 1 дюйм из местного хозяйственного магазина, вы обнаружите, что можете согнуть его одинаково далеко практически в любом направлении (будьте осторожны — эти палки могут внезапно сломаться! ).Но если вы возьмете пиломатериал 2 × 4 дюйма аналогичной длины, вы обнаружите, что если вы попытаетесь согнуть его по 2-дюймовой поверхности, он даст немало — но загрузите его по 4-дюймовому и он будет довольно жестким и жестким. Если вы никогда не строили дом, взгляните на тот, который находится в стадии строительства, и вы увидите, что все балки перекрытия ориентированы таким образом, что нагрузка приходится на пиломатериалы по длине. Это просто заставить большую часть материала работать на вас, выдерживая изгибающие нагрузки и сохраняя жесткость конструкции.
Если бы вы измерили фактическую деформацию лонжерона (или длину 2 × 4) под действием изгибающих нагрузок, вы бы обнаружили, что деревянные пряди на верхней части лонжерона сжимаются, то есть сдвигаются вместе в длинная ось. При этом растягиваются пряди на нижней части лонжерона — они натянуты. Это легко увидеть на прилагаемом рисунке. Интересно отметить, что чем ближе вы подходите к центру (между верхом и низом), тем меньше становятся нагрузки — сжимающие нагрузки сверху и растягивающие нагрузки снизу уменьшаются по мере приближения к центральной или нейтральной оси, лонжерона.
На этом изображении корневого конца лонжерона Xenos показано, как полка крышки «Т» лонжерона входит в слои лонжерона. На корневом конце используются болты для закрепления крышки; когда вы двигаетесь подвесным двигателем, это все заклепки.
Это вряд ли кажется справедливым, не так ли? Волокна в нижней части изо всех сил стараются удерживаться вместе под натяжением, а волокна наверху изо всех сил стараются не раздавиться, но те, что в середине, получают бесплатный проезд! Это осознание того, что мы подошли к первой модификации конструкции «лонжерона плиты», которая представляет собой просто сплошной прямоугольник из дерева. Если средние волокна не берут на себя свою долю нагрузки, что они там делают? Они просто прибавляют в весе, не так ли? Нет ли способа уменьшить эту часть лонжерона и облегчить конструкцию?
Ну, конечно, есть — и так родилась «двутавровая балка». Поскольку большая часть нагрузок приходится на верхний и нижний края, а середина просто слоняется по сторонам, разделяя края, почему бы не сделать среднюю часть более тонкой? Это именно то, что вы видите, глядя на стальную конструкцию, такую как здание или мост: основные элементы конструкции имеют форму буквы «I» в поперечном сечении.Края (крышки) широкие и несущие нагрузку, в то время как середина (или перемычка) предназначена в основном для того, чтобы крышки не сжимались друг к другу.
Лонжерон, выполненный в виде двутавровой балки, подвергает толстый и тяжелый материал крышек под нагрузкой (сжатие сверху, растяжение снизу) и минимизирует материал там, где нагрузка мала (в стенке) .
Полет на двутавровой балке
Поскольку мы начали с дерева, нет причин, по которым мы не можем какое-то время продолжать этот ход мыслей. Деревянные двутавровые балки обычно используются для перекрытий перекрытий и перекрытий в деревянных конструкциях, при этом крышки часто изготавливаются из материала 2 × 4, уложенного на бок, а перемычки — из относительно тонкой фанеры. Лонжероны самолетов могут быть сделаны и делались таким же образом — с силой крыла, находящейся в колпаках, и перемычки, просто удерживающей их друг от друга.
Нет причин, по которым мы не можем применить ту же концепцию к металлическим конструкциям. Типичный алюминиевый лонжерон в наши дни будет построен с отдельными крышками лонжерона — обычно с большим поперечным сечением — и гораздо более тонкими перемычками, часто ламинированными из нескольких листов алюминия.Крышки часто представляют собой алюминиевые стержни или профили определенной формы для распределения изгибающих нагрузок на верхнюю и нижнюю части лонжерона. Некоторые старые цельнометаллические лонжероны, предназначенные для самодельного строительства, были построены из слоев толстого листового металла, который был легко доступен (например, 1/8 дюйма), так что не требовалось специальных профилей или тяжелых заклепок. Если у вас есть один из этих ламинированных лонжеронов, он будет достаточно прочным, но, возможно, не таким легким и эффективным по весу, как новая конструкция со специальными крышками.
Сплошной лонжерон равномерного поперечного сечения (обычно сделанный из дерева) имеет переменную нагрузку сверху вниз. Нижние древесные волокна находятся под напряжением, а верхние — под давлением.
Во многих случаях оптимизированной конструкции лонжероны неоднородны от корня до кончика. Это связано с тем, что чем ближе вы подходите к кончику крыла, тем меньше нагрузка на эту часть крыла и, следовательно, тем меньше вам требуется силы. Крыло Xenos, которое мы используем в качестве примера в этой и будущих статьях, похоже на это.Для очень длинного крыла было бы существенное снижение веса, если бы вы сохраняли одинаковое поперечное сечение от корня до кончика, поэтому при перемещении наружу и полотно, и колпачки становятся менее прочными. Колпачки представляют собой конические экструзии, и полотно использует все меньше и меньше слоев по мере продвижения к кончику. Фактически, полотно в основании состоит из шести слоев материала толщиной до 3/16 дюйма, и это сужается до единственного слоя 0,032-дюймового листового металла к тому времени, когда вы дойдете до середины пролета.
Слово о композитах
Композитные крылья подчиняются тем же законам физики и механики, что и металлические конструкции, и то же самое относится к их лонжеронам, но они могут выглядеть немного иначе.Вы по-прежнему будете видеть составные лонжероны, которые выглядят как двутавровые балки, встроенные в крылья, но, поскольку конструктор обладает большой гибкостью при наложении слоев ткани, которая идет в крылья, иногда структура лонжерона сливается с обшивкой крыла, что не совсем так. очевидно. Интегрированный структурный дизайн помещает прочность именно там, где она нужна проектировщику, и вы найдете конструкции без очевидного лонжерона вообще, но можете поспорить, что они спроектированы с необходимым слоем для обеспечения желаемой прочности в правильном направлении.
Когда лонжероны становятся особенно толстыми возле корня, фланцы нервюр необходимо приклепать к узлу при сборке лонжерона. Зажимы на этом лонжероне будут удерживать внутренние нервюры.
The Web
Возвращаясь к алюминию: Как упоминалось ранее, материал лонжерона служит в первую очередь для того, чтобы удерживать крышки друг от друга и предохранять лонжерон от разрушения. С чисто структурной точки зрения это верно, но в реальном мире это гораздо больше.Наверное, самое очевидное — ребра можно крепить к полотну. В более старых самолетах из каркаса и ткани обычно используются цельные нервюры, которые скользят по лонжерону (некоторые металлические самолеты также используют эту конструкцию) к своим местам, где они крепятся. В наши дни нервюры чаще состоят из нескольких частей: одна перед лонжероном, а другая — сзади. Эти две детали приклепаны к лонжерону в месте их встречи.
Стенка типичного металлического лонжерона состоит из нескольких слоев, количество которых уменьшается по мере приближения к кончику, где меньше нагрузки. У Xenos ножка лонжерона входит в паз наверху.
Стену также можно использовать для крепления таких вещей, как шкивы троса управления или коленчатые рычаги. В этом случае полотно часто укрепляется удвоенной пластиной, чтобы сделать его локально более жестким для восприятия боковых нагрузок, создаваемых элементами управления. Лента может также поддерживать монтажную конструкцию топливного бака, а также кабельные каналы или зажимы.
Говоря о проводке, строители нередко спрашивают, могут ли они пропустить проводку через крыло спереди назад, пробив лонжерон.Это хороший вопрос для дизайнера, но к настоящему моменту вы должны понять, что, поскольку центр полотна обычно не несет нагрузок сжатия или растяжения, отверстия в полотне около середины обычно не являются проблемой. Опять же, посоветуйтесь со своим дизайнером, чтобы убедиться в этом, но если вы не можете понять, почему допускаются отверстия в лонжероне, понимание пути нагрузки должно вас успокоить. Это, конечно, не дает вам карт-бланш на просверливание столько отверстий, сколько вы хотите в любом месте вашего лонжерона, но это объясняет, как и где это нормально.
Заглушки
Заглушки лонжерона, как уже упоминалось, могут быть выполнены из профилей особой формы и с конусом или из простых прямоугольных блоков алюминия, в зависимости от того, как проектировщик хочет оптимизировать вес лонжерона и насколько доступны детали. Строители самолетов, построенных по плану, обычно хотят иметь возможность покупать стандартное сырье. Для комплектов можно использовать нестандартные материалы, если строители понимают, что завод, вероятно, будет единственным источником запасных частей. Колпачки лонжеронов, как правило, непрерывны от корня до кончика, поэтому повреждение одной во время строительства может означать дорогостоящую доставку при длительной замене.На Xenos каждая крышка имеет длину около 25 футов. Доставка по стране обходится недешево, так как его нужно хорошо упаковать, чтобы не гнуть.
Обращаться с колпаками лонжеронов важно осторожно, поскольку они являются конструктивными элементами, которые действительно удерживают вас в воздухе. Элементы, находящиеся в состоянии растяжения, растягиваются и не подвержены короблению, но сжатые элементы (обычно верхняя стенка при горизонтальном полете) сжимаются. Если вы когда-либо опирались на пустую банку из-под газировки, а затем стучали по сторонам, чтобы она мгновенно схлопывалась, вы испытали отказ из-за деформации сжатия.Подумайте об этом в следующий раз, когда увидите вмятину на лонжероне. Может быть, эта дорогая стоимость доставки не так уж и плоха … а?
Сверление отверстий в крышках, отличных от тех, которые требует проектировщик, запрещено. Обращайтесь с ними осторожно и проделайте все отверстия в соответствии с чертежами и спецификациями. Следует просверлить плотно прилегающие отверстия и расширить их до нужного размера. Увеличенные или продолговатые отверстия — повод для отказа. Точно так же зазубрины и впадины — держите эти крышки в чистом виде, и вы сможете быть уверенными в 3 (или более) G, когда вы летите.
Скрепление вместе
Большинство алюминиевых лонжеронов склепаны вместе, при этом болты часто добавляются в толстых местах, потому что установка заклепок диаметром более 5/32 дюйма затруднительна, а в некоторых местах требуется прочность стального болта. Чаще всего болты используются возле корня, где нагрузки самые высокие. Деревянные лонжероны часто имеют стальные стыковые пластины и болты возле корней по тем же причинам: общая нагрузка на лонжерон велика у корня, и материал должен быть усилен, чтобы обеспечить достаточный запас.В любом случае важно использовать фиксаторы, указанные дизайнером, и не допускать замен без явного разрешения.
Конечно, крылья в конечном итоге должны быть прикреплены к фюзеляжу, чтобы они работали вместе с хвостом и двигателем, создавая летающий самолет. Лонжероны являются основными точками крепления, поскольку они несут нагрузку, и многих новичков удивляет, сколько болтов нужно, чтобы удерживать крылья. Или, в случае некоторых самолетов, сколько! Старый Cub обычно имеет только один болт, удерживающий корневой конец основного лонжерона для каждого крыла, а также один болт для заднего лонжерона.Затем стойки крыла прикручиваются болтами к середине размаха на верхних концах и к нижнему лонжерону фюзеляжа на внутреннем нижнем конце. Эта треугольная ферма довольно прочна при положительной нагрузке (не так сильно при отрицательном G), а болты довольно большие.
Типичный самолет с низкорасположенным крылом будет иметь укороченный лонжерон как часть конструкции фюзеляжа — секцию, построенную, как и остальная часть основного лонжерона, такую же толстую и массивную, как корневую секцию, но надежную часть конструкции фюзеляжа. Ножки лонжеронов крыла затем будут перекрывать лонжерон центральной секции цоколя и прикрепляться к нему болтами большого диаметра, достаточными для жесткой фиксации крыла на месте.Это устанавливает двугранный угол конструктора и создает консольную конструкцию, не требующую распорок. Многие металлические самолеты не имеют такой массивной центральной секции, но корни лонжеронов доходят до центра фюзеляжа и крепятся болтами к металлической коробке со стальными стыковочными пластинами и множеством болтов, по сути, образующих единое целое. крыло от кончика до кончика, когда все крепления установлены.
Планеры и другие летательные аппараты часто имеют лонжероны, которые не только входят в фюзеляж, но и полностью пересекаются с другой стороной фюзеляжа, перекрываясь своим сопряженным крылом и скрепляются вместе болтами, снова образуя то, что по сути является одним — штучное крыло, с прикрепленной конструкцией фюзеляжа.Xenos такой же, и для его скрепления требуется всего пара (больших) болтов.
Конструкция — это конструкция, а методы проектирования включают вычисление нагрузок — и иногда пилот просто должен доверять расчетам проектировщика, когда поднимается в воздух, когда он видит, как конструкция кажется скрепленной вместе с небольшой видимой прочностью. Я был удивлен, когда снял крылья с оригинального RV-1 Ван, и обнаружил, что между крыльями и центральной секцией нет никакого перекрытия — верхняя и нижняя крышки имели отверстия на концах, которые входили в проушины в центральной секции стальной фермы. , и скреплялись (сверху и снизу) с помощью одного конического стального штифта. Задний лонжерон крепился к фюзеляжу одним болтом — и все. И это был полностью пилотажный самолет, рассчитанный на выдержку 9 G.
Pulling for Flight Loads
Главный лонжерон — это то, о чем мы говорили до сих пор, но он не работает один. Не менее важное значение имеет задний лонжерон. Меньший по размеру, чем основной лонжерон, задний лонжерон удерживает выравнивающие нервюры и обшивку и крепится к фюзеляжу, предотвращая перекос конструкции крыла. Он также создает коробчатую конструкцию с передним лонжероном, чтобы реагировать на нагрузки, которые заставят крылья стремиться к обратному движению.Для деревянных крыльев нередко можно увидеть компрессионные стойки и проволоку, предотвращающую лобовое сопротивление, между передним и задним лонжероном, чтобы придать жесткость конструкции, создавая небольшие треугольные фермы в раме, чтобы сделать очень прочную, но легкую конструкцию.
Консольные крылья являются обычным явлением в наши дни в высокопроизводительных самолетах, потому что отказ от подкосов избавляет от большого сопротивления, но строители по-прежнему строят множество самолетов, похожих на Cub, с выступающими стойками — и они являются важной частью уравнения прочности любого крыла. Вы не могли бы использовать деревянный лонжерон крыла Cub в консольной конструкции, потому что он просто не может выдержать нагрузку без помощи подкосов. Точно так же консольные деревянные крылья имеют очень глубокие и прочные лонжероны, компенсирующие отсутствие распорок. И как только мы попадаем в составной мир, у нас нет предела: поскольку нагрузки могут распределяться по интегрированной структуре, требуется совершенно новый взгляд на нагрузки.
Типичная часть лонжерона Xenos показывает колпаки лонжеронов (желтым цветом), перемычку лонжерона (послойно посередине) и зажимы, которые будут действовать как точки крепления нервюр во время сборки крыла.
Xenos Spar
Эта статья наклонена в сторону металлических крыльев и лонжеронов, потому что в следующий раз мы начнем подробно рассматривать конструкцию типичного металлического лонжерона, предназначенного для мотоплана Xenos. Более длинный, чем вы ожидаете от типичного спортивного самолета, он достаточно велик, чтобы показать примеры различных деталей, которые вы найдете на любом металлическом лонжероне, и является хорошим примером того, как нагрузки — и, следовательно, структура — изменяются при вы идете от корня к кончику. Паутина тщательно состоит из разных слоев, которые уменьшаются от корня до кончика, и на ней есть специальные места для установки органов управления и большие рычаги для тормозов.Он также сконструирован с тщательно суженными крышками лонжеронов, сверху и снизу. Вся конструкция скрепляется 5/32-дюймовыми заклепками, их длина и тип меняются по мере движения вниз по конструкции. Заклепки заподлицо необходимы около корня, где два лонжерона перекрывают друг друга в фюзеляже, а заклепки с полукруглой головкой используются в других местах, потому что их можно быстро установить без необходимости зенковки и углублений.
В лонжеронах Xenos есть всего понемногу (кроме композитных материалов), и мы приглашаем вас следить за нашим продолжением исследования сердца крыла — главного лонжерона.
Super Rib Jig — Chris ‘Acroduster Too
Большинство строителей используют простое деревянное приспособление с деревянными брусками для установки фиксирующей полоски. Проблема здесь в том, что при использовании клея / эпоксидной смолы древесина прилипает к дереву.
Еще я заметил, что большинство строителей строят только одну сторону ребра за раз. Они кладут свои части в приспособление, затем кладут косынки на верхнюю часть и прибивают или скрепляют их на месте, пока клей не высохнет.Затем они должны удалить ребро, перевернуть его и повторить процесс установки косынки. Затем необходимо удалить все гвозди или скобы. Затем процесс повторяется, пока не будут сформированы все ребра.
Друзья есть решение! Приманка Super Duper Wonder! Никаких гвоздей! Никаких скрепок! Никакой вощеной бумаги! Больше не нужно заниматься по одной стороне за раз! Как спросите? Что ж, пусть всемогущий Крис разъяснит вам решение.
Стекло Plexi — это ответ! Т-88 к нему не прилипнет. Начните свою джигу с фанеры хорошего качества или искусственной древесины.

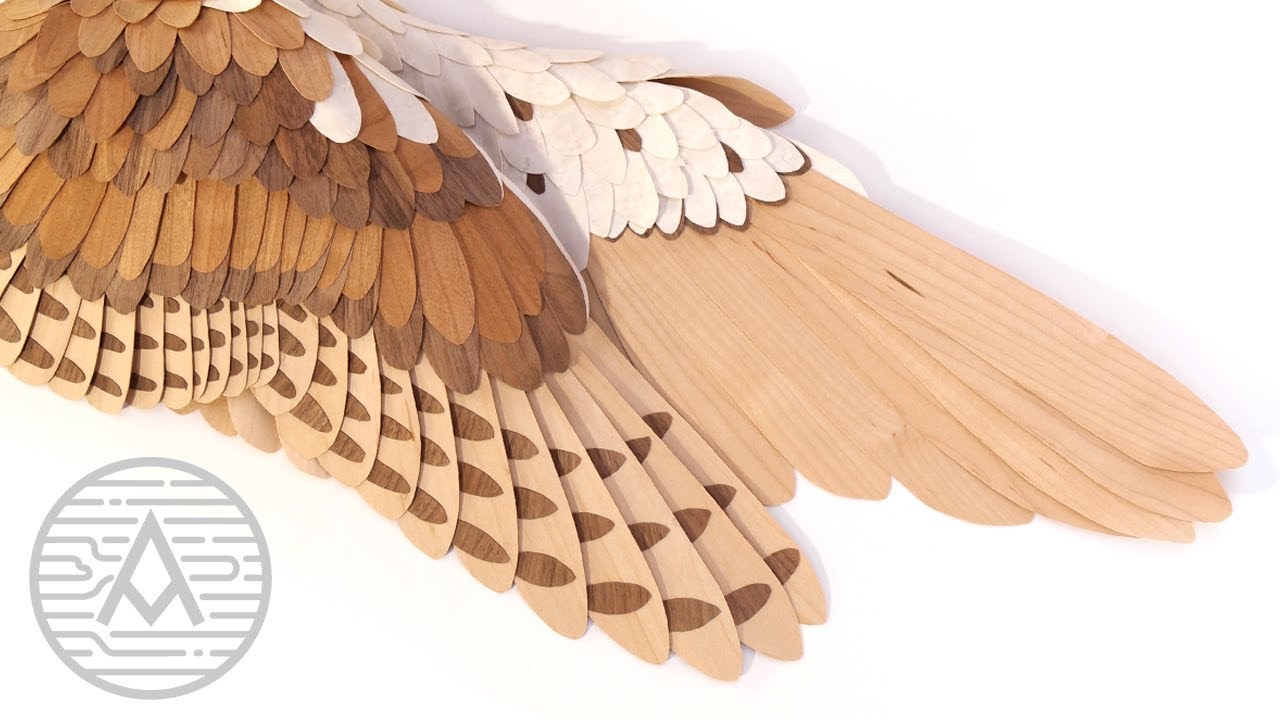
Теперь вам нужно будет просверлить зажимное приспособление там, где будут находиться все ваши косынки, чтобы, когда ребро будет выполнено, ваши дюбели надавили на косынки, чтобы «вытолкнуть» ребро из зажимного приспособления.Просверлите отверстия на 1/16 больше, чем дюбели, чтобы не было помех.
Теперь вам нужно будет перенести эти отверстия на верхнюю часть вашей верхней части, только из фанеры, чтобы вы могли приклеить свои деревянные дюбели (как показано на рисунке выше). Когда это будет завершено, вам нужно будет сложить обе части приспособления вместе, чтобы вы могли просверлить в них 3-4 отверстия для ваших болтов. Болты будут удерживать половинки вместе, пока клей высохнет. Я использовал лаг на 3/8 дюйма. болты с крыльчатыми шайбами и барашковыми гайками.Стяжные болты постоянно монтируются в базе зажимного приспособления. Таким образом, когда вы кладете верхнюю часть на болты, они будут использоваться в качестве направляющих, и верхняя часть будет плавно скользить вниз на место.

Теперь у вас есть замечательный инструмент, который сэкономит вам бесчисленное количество часов при наращивании ребер. Не нужно будет использовать гвозди или скобы, и вы сможете вставлять ластовицы с обеих сторон одновременно. Когда вы «выдвинете» ребро, оно будет готово к шлифовке и покрытию лаком.
Вот как это сделать!
Поместите все детали в шаблон, включая косынки с обеих сторон.
когда вы довольны посадкой, приклейте все. Сначала положите все косынки клеевой стороной вверх. затем положите туда все свои палочки, а затем верхние косынки. Теперь вы надеваете верх и затягиваете барашковыми гайками. Их не нужно затягивать, их нужно просто прижимать. Т-88 не требует прижимного усилия.
Вы можете увидеть ребро, расположенное между зажимным приспособлением. После того, как клей застынет, в течение ночи или примерно через 8 часов, вы просто снимаете верхнее приспособление и кладете его на стол.Затем возьмите приспособление с ребром в нем и надавите на дюбели, чтобы «выдвинуть» уже готовое ребро.

С помощью этого приспособления вы найдете удовольствие в изготовлении ребрышек. После того, как он будет снят с приспособления, он станет готовым ребром! Больше никогда не тянуть за гвозди! Как сказал мне друг, «Сделать ребра из этого так же просто, как пнуть цыплят в ручье»
Наслаждайтесь и получайте удовольствие.
Сделайте деревянный игрушечный самолетик — Деревообработка для простых смертных
Чтобы запустить программу Makers Care и собрать деньги для фонда Make-A-Wish Foundation, мы просим вас сделать самолет.Он не обязательно должен быть деревянным: вы можете сделать его из всего, что захотите! Мы просто хотим, чтобы вы участвовали.
Узнайте больше о Makers Care и примите участие на сайте MakersCare.org.
Как сделать деревянный игрушечный самолетик. Два варианта!
Я не мог решить, хочу ли я, чтобы мой самолет был одинарным или бипланом, поэтому сделал и то, и другое! По сути, они имеют одинаковую конструкцию: для биплана нужно просто добавить верхнее крыло и соединительные стойки. Бесплатные планы для обеих версий (в британской и метрической системе) доступны здесь.
Я использовал древесину 3/4 ″ (18 мм) из своего мусорного ведра. Этот проект идеально подходит для ленточной пилы. Если у вас ее нет, воспользуйтесь лобзиком. Для более тонких крыльев и пропеллера я предлагаю использовать фанеру толщиной 1/4 дюйма (6 мм).
Загрузив шаблон для резки, вырежьте части и приклейте их к пиломатериалам с помощью клея-распылителя.
Затем вырежьте формы из плоских частей.Их будет четыре: фюзеляж, крыло (для биплана оно будет распилено на две части), хвостовое крыло и пропеллер.
Если вы делаете одностворчатый самолет, то теперь вы можете разделить дерево на две части. (Вы будете использовать только половину с наклеенным шаблоном). Опять же, вы можете просто использовать тонкую фанеру, если не хотите разделять доску пополам.
Если вы собираетесь сделать биплан, просверлите отверстия для распорок, прежде чем разделить доску пополам. Таким образом, вам нужно будет сделать только четыре отверстия вместо восьми, и они будут идеально совмещены, когда вы прикрепите их дюбелями.
Отшлифуйте все детали гладко. Не отклеивая шаблон, вы можете шлифовать детали прямо до линии.
Обязательно отметьте, где вам нужно будет просверлить отверстия под дюбели опоры колеса. Таким образом, вы сможете найти их, когда бумажный шаблон будет снят.
Я использовал свой маршрутизатор, чтобы скруглить края фюзеляжа.
Если у вас нет фрезы, вы можете отполировать острые края с помощью шлифовки. Крылья пришлось отшлифовать, потому что у меня нет достаточно мелких округлых насадок, чтобы работать с тонкой древесиной.
С помощью сверлильного станка просверлил два отверстия под колесные опоры. Для биплана я просто просверлил отверстия насквозь.
Затем просверлил отверстие под ось в каждом дюбеле опоры колеса.
Я вклеил их в отверстия на крыльях и убедился, что отверстия для оси оси совпадают.
Приклейте хвостовое крыло на место.
Для биплана приклейте четыре стойки и соберите крылья.
Наклейка на крылья.
Приклейте колеса к оси, следя за тем, чтобы клей не попал на опоры колес. Я использовал колеса, купленные в магазине товаров для рукоделия. Это проще, чем пытаться сделать самому.
Затем отрежьте концы оси.
Просверлите отверстие в носовой части самолета и с помощью винта прикрепите пропеллер.
Я закончил свои самолеты аэрозольным лаком, но было бы тоже весело их покрасить!
Бесплатные планы:
| Комплекты крыльев Наши комплекты крыльев с ЧПУ производятся в соответствии со строгими стандартами. «Я очень доволен и настоятельно рекомендую этот комплект всем, кто заинтересован в создании Skybolt …» «Мой комплект крыльев прибыл, как и было обещано, и качество изготовления безупречное …» «У вас отличные комплекты крыльев! …» «Спасибо за комплект крыльев и супер поддержку».
|
|
Строительство крыла самолета из бальзового дерева
Этот учебник документирует строительство внешнего крыла. панель для радиоуправляемого самолета.Используемые техники общие для бальзовой модели.
здание в целом. Вы начнете с набора бальзовых деталей,
план и немного клея. Если детали еще не вырезаны из дерева,
шаг, очевидно, идет первым.
(При необходимости перенести чертежи деталей в дерево, сначала см. этот учебник).Нажмите на миниатюры, чтобы увидеть увеличенное изображение.
Самый распространенный инструмент для резки бальзы — X-acto нож с лезвием №11, показанный на левом рисунке. Не забывай свой безопасные очки! Используйте старый журнал или другую поверхность в качестве разделочной доски. Примерно через двадцать минут с острым лезвием и ребра все готово:
Теперь подготовим поверхность здания. Вам нужна квартира
стол или верстак.Некоторые используют лишнюю дверь на двух козлах.
Проверьте с помощью длинной линейки, чтобы она была плоской.
Будем использовать булавки чтобы закрепить детали во время сборки, покройте поверхность акустической потолочной плиткой (Home Depot, и т. д.), см. левое изображение ниже. Затем разместите развернутый план на потолке. плитка. Затем закрепите липкой лентой (или булавкой) вощеную бумагу (или саранскую основу), чтобы защитить бумажные планы от натиска клея:
Теперь начните строить прямо над планом, располагая детали над их расположением на плане.Точная последовательность будет отличаться в зависимости от вашего комплекта или инструкций по плану, но вот типичный. Lay нижний лонжерон и заднюю кромку на плане, приколоть их на место (фото слева).
Затем установите ребра крыла на место, приклеивая их тонким клеем СА. Использовать
клей экономно: небольшое количество подойдет; слишком много добавляет лишний вес
и течет повсюду, что усложняет шлифовку. Пытаться
чтобы ребра были вертикальными (используйте треугольник под углом 90 градусов).Затем установите и приклейте
верхний лонжерон и передняя кромка:
На этом этапе крыло было достаточно прочным, чтобы его можно было снять с план и начало деревянного настила. Переверните крыло и сделайте верх защитное покрытие, затем снова переверните и добавьте нижнее покрытие. Используйте клей CA.
Теперь ни одна сборка не будет идеальной, вы получите несколько пробелов, вмятины или выбоины. Здесь есть промежуток между защитным покрытием и ведущим край крыла.Обшивка может двигаться здесь вверх и вниз, уменьшая крыло. прочности и препятствует качественной шлифовке и покрытию.
Лучше всего заделать зазоры деревом, если возможное; дерево намного прочнее (на единицу веса) клея или шпатлевки!
В
на среднем фото ниже я вставил тонкие полоски дерева (наклеенные желтым
клей, будет легче шлифовать, чем клей CA). Затем защитное покрытие удерживается на месте
с лентой.
После высыхания клея и шлифовки поверхности окончательная зазоры заполним легкой шпаклевкой (фото справа).Ванна на 8 унций материал прослужит во многих моделях:
Теперь нам просто нужно добавить блок подсказки, чтобы завершить панель крыла. Копировальная пила или пила X-acto (красная ручка) быстро справятся с задачей бальзового блока. Также необходимы шлифовальные блоки (80 и 220). и респиратор от пыли. Ребро на конце нуждается в шлифовании защитного покрытия и лонжеронов. промывка, сделайте это в первую очередь:
Затем приклейте блок наконечника на место.Покройте всю концевое ребро с тонким слоем желтого клея, затем скотчем или булавкой на место, пока оно сохнет. Отметьте очертание кончика крыла на блоке, затем с помощью пилы срежьте лишняя древесина. Десять минут распиливания дали показанный грубый наконечник (второе фото справа), и некоторое время с двумя шлифовальными блоками приводило к довольно гладкая отделка (фото справа):
Теперь шлифуйте всю секцию крыла постепенно
наждачная бумага более мелких сортов (крепится к блокам).