Изготовление деревянного крыла – Как сделать пластиковые крылья самолету своими руками
Как сделать пластиковые крылья самолету своими руками
Выбор проекта в пользу KR2S пал не просто так. В начале 2006 года мой коллега и я планировали построить полнопилотажный тренажер самолета, поскольку оба были фанатами MS Flight Simulator. Харди, по профессии инженер, имел талант находить старым вещам новое применение. Так мертвый видеомагнитофон и двигатель от стеклоочистителя могли стать основой для системы подвижности авиатренажера. Но после небольшой прикидки на размер бюджета мы выяснили, что стоимость нашей задумки может превысить 10000$.
Во время поисков информации в Интернете на тему подвижных авиатренажеров, я случайно наткнулся на статью о самолете стоимостью в 10000$. Это был KR2S, и эта была любовь с первого взгляда. Именно этот самолет я мог сделать своими руками, он стоил меньше симулятора и мог помочь мне продолжить мои летные уроки.
Кроме характеристик и внешнего вида самолета, меня привлекло сообщество KR строителей, которое располагала к себе в плане помощи решения сложных вопросов во время строительства. Всегда можно было рассчитывать обратиться за поддержкой к тем, кто уже прошел этим путем.
KR2S, задуманный мной, был маленьким самолетом с хвостовым колесом и с ламинированным гнутым лонжероном. На страницах этой статьи вы найдете описание опыта постройки этого самолета, вместе с полезными советами решения разных задач. И это будет моя версия того, как построить Rand Robinson KR2S.
Так описывает начало своего увлечения строительством самолёта Дарен Клутенг-Кромптон из Австралии, оригинальную подборку статей которого на тему строительства KR2S можно найти на английском языке на сайте www.kr-2s.com.
Формирование стеклопластиковой обшивки крыла
Центральная часть крыла крепится непосредственно к фюзеляжу самолета. К двум лонжеронам, выходящим из фюзеляжа, крепится консоль крыла и все остальные его элементы. Внутреннее пространство между лонжеронами и нервюрами позволяет разместиться топливному баку, узлам управления и проводке навигационных огней. Наружная обшивка формирует профиль крыльев, предохраняет органы самолета от повреждения, а также создает прочностную основу самолета, поэтому к её изготовлению следует подойти внимательно.
Толщина обшивки крыла определяется по заранее построенным контурам на нервюрах. В данном случае линия 3/8” определяет контур будущей обшивки. На фотографии скреплены с помощью степлера два шаблона нервюр: с хордой 44″ (дюйма) и с хордой 48”. По этим контурам определяется толщина наружной обшивки.
Внутрь крыла, отмеченного лонжеронами и нервюрами, кладется кусок пенопласта толщиной 2”. После чего края пенопласта срезаются по границам контуров на нервюрах.
Пенопласт затем извлекается, а по отмеченной линии рубанком аккуратно срезаются излишки пенопласта.
Процесс выполняется до получения ровной поверхности.
Так, что после установка обшивки, её границы точно соответствуют границам ранее отмеченных контуров на шаблоне, в данном случае 3/8”.
Предварительная подготовка места под укладку слоя обшивки включает в себя подвязку ремней, чтобы обшивка не упала на гаражный пол, а также изоляцию места монтажа полиэтиленовыми пакетами для улучшения адгезии.
Стеклоткань заготавливается вне места укладки. Заготовкой служит простой стеклотканевый лист. Кстати, стеклоткань кладется на пенопласт под углом 45° по направлению хорды крыла.
Такой сэндвич затем помещается внутрь крыла и предохраняется ремнями от падения. Также можно использовать дополнительные пластины, бруски из дерева и прижимы.
Установка топливного бака
После полимеризации и извлечения «пирога», с лонжеронов были сняты шаблоны нервюр. Для облегчения нервюр на шаблонах с помощью дрели с насадкой было сделано несколько отверстий, при этом было обеспечено достаточное минимальное расстояние между отверстиями и кромками крыла в пределах 1,5” для прочности. После этой операции нервюры стали весить на 280 граммов легче.
Ширина углубления на шаблонах оказалась не достаточной для установки на лонжероны, так что лонжерон пришлось зашкурить.
После монтажа обшивки на место, приходит самое время для изготовления опор топливного бака. Опоры приклеиваются эпоксидной смолой с наполнителем к обшивке.
Интересная операция выполняется перед монтажом бензобака на опоры: на опоры топливного бака между ним и бензобаком временно кладется наждачная бумага.
Топливный бак помещается сверху на обшивку и фиксируется в этом положении, после чего наждачная бумага извлекается. Данная процедура позволяет подогнать контуры опор под основание бензобака.
Сверху на пенопластиковые ребра помещается очередной слой стеклоткани с небольшим содержанием эпоксидной смолы. В тех местах, где слой не сажается до конца, пенопласт дорабатывается. После полимеризации кромки и углы ребер становятся по-настоящему крепкими.
Прежде чем использовать стеклоткань для крепления нижней обшивки, каждый лонжерон был обмазан клеем в трех местах. Это укрепило место установки топливного бака перед монтажом обшивки на длительное время.
Установка топливного бака была выполнена также по шаблону.
Стеклоткань кладется на внутреннюю часть обшивки стандартным способом, а жертвенная ткань лежит сверху, чтобы впитать излишки смолы. Вся операция выполняется на верстаке, а время сушки примерно час. Стеклопластик довольно липкий и податливый, поэтому, когда обшивка переворачивается, она все ещё остается достаточно мокрой, чтобы прилипнуть к слою жертвенной ткани. Как только форма обшивки сформирована, верхняя часть все еще остается плоской. Чтобы отвердевание прошло успешно сверху кладется доска и зажимается струбцинами.
Как только внутренняя часть обшивки отвердевает наступает время добавить еще несколько слоев стеклоткани, как и в случае с нижней обшивкой. Это поможет прочно зафиксировать топливный бак в продольном направлении крыла.
Так выглядит внутренняя часть верхней обшивки с установленными ребрами жесткости в продольном направлении крыла.
Изготовление носовой кромки
Чтобы собрать носовую кромку достаточно 2 кусков 2” пенопласта, которые собираются в секцию по контурам нервюр от 3/8” до ½”. Получается пакет V-образной формы.
Крепежные узлы на лицевой стороне переднего лонжерона закрываются изолентой.
Однослойный кусок стеклоткани помещается внутри передней кромки из пенопласта. После сглаживание морщин в жертвенной ткани концы пакета скрепляются степлером для того, чтобы кусок стеклопластика оставался прочным. Далее вся конструкция оставляется на час, чтобы стеклопластик прочно прилип к пенопласту.
Через час передняя кромка устанавливается в нужное место напротив основного лонжерона, пока не отвердеет окончательно.
Лишний пенопласт необходимо ободрать рашпилем и зачистить шкуркой по шаблону.
Один из вариантов -ободрать пенопласт с передней кромки, для этого можно использовать асфальт.
Вот так выглядит центральная часть крыла после зашкуривания. В целом поверхность можно доработать шкуркой до идеальной формы или близкой к ней.
Контуры листа стеклоткани под вырезание отмечаются прямо по форме передней кромки.
Ночи бывают холодными, и вырезанный кусок стеклопластика плохо будет абсорбироваться с жертвенной тканью на утро. Для того чтобы его согреть и сделать более податливым, можно использовать 500 Вт лампу.
Утром сэндвич из стеклоткани и жертвенной ткани кладется на переднюю кромку, предварительно установленную по месту.
На следующий день сэндвич легко снять, если заранее побеспокоится о применении клейкой ленты. Доводку передней кромки можно оставить до момента завершения строительства крыла.
Изготовление хвостовика и его обшивки
Хвостовик крыла также формируется с помощью слоенного пирога. В качестве основы используется вырезанный по шаблону кусок пенопласта. Его поверхность должна получиться ровной без изъянов от начала до конца.
Обе внутренние поверхности, формирующие хвостовик, будут состоять из одного слоя стеклоткани.
Лучший вариант по вопросам удобства – приклеить шаблоны вместе с сосновыми клиньями. Такая конструкция жестко устанавливает размер.
Поскольку данная деталь будет закрылком, удобнее изготовить её отдельно от остальных. При монтаже она устанавливается вдоль контура ½” с помощью струбцин и раздвижного зажима. Низ подвижной створки зачищается по шаблону.
Острая кромка также зачищается по шаблону.
Эпоксидный клей и углепластик также наносятся на пенопласт. Операция выполняется на рабочем столе: всё фиксируется и остается сохнуть на два часа. Так что пластиковая обшивка не будет слезать, но в то же время останется достаточно податливой, чтобы позже её можно было выравнять.
На фото снизу также можно увидеть алюминиевый уголок, стеклоткань вместе с жертвенной тканью.
Откидная крышка также будет вращаться на рояльных петлях.
Так закрылок будет выглядеть в нижнем положении.
Процесс ошкуривания пенопласта до толщины 3/8” начинается с покрытия обеих сторон эпоксидной смолой. После ряда подобных операций пластинка становится очень твердой и легко обрабатываемой.
Поверхность закрылка укреплена диагональным ребром жесткости, это сделано для того, чтобы уменьшить любое торсионное скручивание при вращении. В то время как у кого-то может возникнуть желание облегчить конструкцию за счет дополнительных ребер жесткости, было принято решение также усилить составной бандаж в центре дополнительным ребром с креплением к лонжерону.
После работы над закрылком приходит время заняться установкой топливного бака и его подключением к топливной системе.
Если перебрать с наполнителем, то можно увидеть, как пена, похожая на тесто, будет лезть из всех щелей, а сам процесс извержения может затянуться до 30 минут. Что касается наполнителя, то его можно приобрести в строительных магазинах. Для бензобака может наполнитель для утепления крыш под маркой DIVINYCELL.
На этом этапе должно также состояться ваше знакомство с проводкой. От топливного бака необходимо будет провести провода: красный с положительным зарядом и белый провод с отрицательным. Для фиксации проводов используются либо кабельные фиксаторы, либо жидкие гвозди.
Расширяющийся наполнитель некоторое время будет просачиваться в промежутке между топливным баком и задним лонжероном, так что понадобиться мелкий рашпиль и около 45 минут работы для надежного удаления излишек.
Прежде чем установить заднюю обшивку на место, все болты и гайки стоит затянуть и покрыть эпоксидной смолой в качестве «контровки».
Это верхний слой обшивки с мокрыми углеродными волокнами. Он готов к перевороту и применению на лонжеронах и фанерных профилях.
Внутренняя часть верхней обшивки покрывается эпоксидным клеем в местах сопряжения с лонжеронами.
Доделка проекта
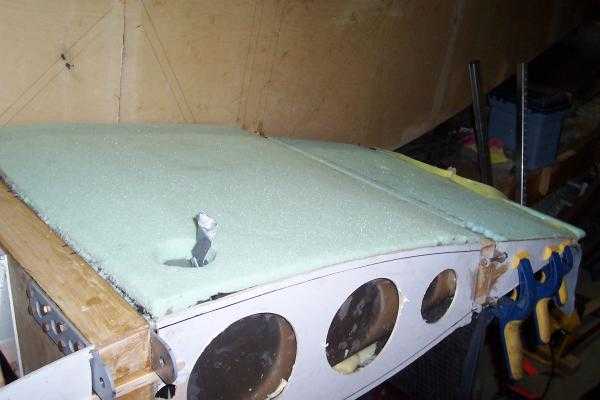
Основная обшивка была отягощена преднамеренно деревяшкой и куском рельсы для того, чтобы остановить «кипение пены» и возможного поднятия обшивки. Если внимательно присмотреться, то можно увидеть, что из горловины бака торчит ручка. Она облегчит снятие обшивки, когда процедура будет завершена.
Через сутки профиль зашкуривается наждачной бумагой, закрепленной на доске, размерами 4” на 1”.
Съемная трубка Пито выглядывает наружу из-за передней кромки. В том месте пенопласт был удален и вместо него был приклеен кусочек древесины. В кусочке дерева есть просверленное отверстие, куда вставляется трубка для замера скорости. Вокруг трубки лента для адгезии, так что смола не будет липнуть.
Вот так выглядит передняя кромка сзади: кусок древесины с просверленным отверстием посередине и трубка ПВХ, впаянная в это отверстие.
От датчика скорости идет воздушная трубка диаметром 5/8”, опоры которой вмонтированы в переднюю кромку.
Количество навигационных огней к моменту написания статьи не было известно точно, поэтому были проведены три пары проводов 16G Tefzel и одна пара 14G. Одна пара 16G используется для датчика топливного бака, другие две идут на стробы (на законцовках крыльев огни против столкновений) и навигационные огни. Все провода идут к блоку, смонтированному на главном лонжероне. Они промаркированы лентами разного цвета на концах.
ПВХ трубки защищают провода от истирания в отверстиях через ребра жесткости или фюзеляж. Каждый раз, когда провода находятся в соприкосновении с металлическими частями, они изолируются дополнительными ПВХ трубками или резиновыми прокладками.
На фотографии запечатлен момент установки передней кромки на лонжероны и нервюры. Самолет KR вывезен из гаража и перевернут вверх тормашками. Для окончательного приведения в норму поверхности были еще раз ошкурены и очищены пылесосом.
Сходный процесс изготовления обшивки используется для низа самолета. Прежде всего, в пластике делается прорезь для устан
1aviaclub.ru
Как делают крылья для самолёта » Военное обозрение
3 месяца назад, 28 мая 2017 года, совершил свой первый полёт российский ближне-среднемагистральный среднефюзеляжный пассажирский самолёт МС-21 «Иркут». Он успешно отлетал полчаса и на этот год уже запланировано начало серийного производства. Вроде бы всё обычно, но только с первого взгляда. МС-21 не зря расшифровывается как «Магистральный самолёт XXI века».Сейчас я вам расскажу, что необычного в этом самолёте.
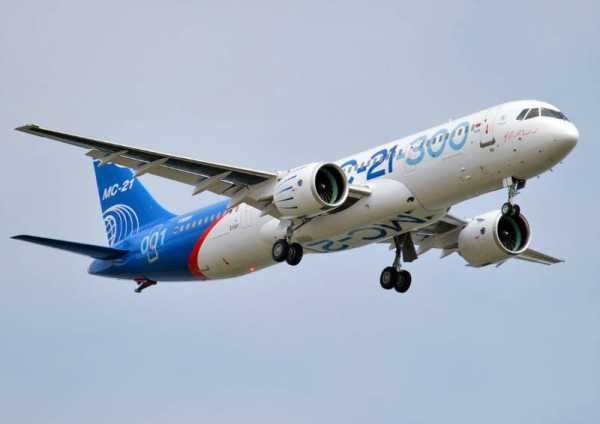
Ноги, крылья… Главное — хвост!
1. Самое необычное в МС-21 — крылья и несколько других деталей силовой конструкции. Они изготовлены из полимерных композитных материалов (ПКМ). В мире сегодня существует только три самолёта с такими крыльями: Boeing 787 Dreamliner, Airbus A350 XWB и Bombardier CSeries.
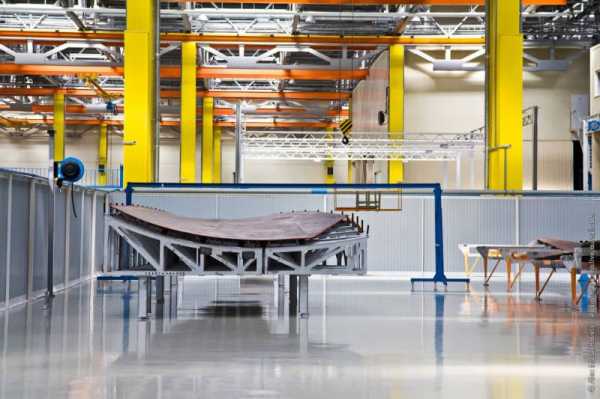
2. ПКМ — это несколько слоёв углеволокна, скреплённого между собой специальной смолой. Чем же так хорош этот материал? Во-первых, прочность углепластиков выше чем у алюминия в 6-8 раз, а удельный вес — ниже в 1,5 раза. Использование ПКМ при производстве космической и авиационной техники позволяет сэкономить от 5 до 30% веса летательного аппарата. Во-вторых, крыло самолёта из ПКМ условно состоит из 10 элементов, а из металла — из 100. Можно понять, монтаж какого крыла обходится дороже.
Производят такие крепкие и ультрасовременные крылья для МС-21 в Ульяновске. Завод называется «АэроКомпозит» и находится на территории «Авиастара». Давайте заглянем за проходные и посмотрим, как выглядит это производство.
Первое, что поражает — это огромные и стерильно чистые цеха! Производство углепластика не терпит грязи, ведь попадание инородных включений в массу грозит снижением прочности всей конструкции крыла.
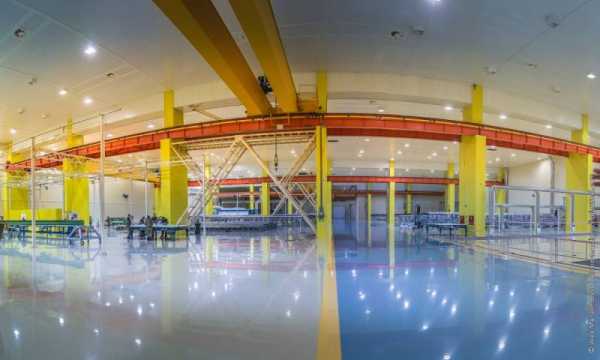
Как это сделано?
3. Процесс изготовления кессона крыла состоит из нескольких этапов. Сначала подготавливается поверхность нужной формы, на которую будет выложено углеволокно. На «АэроКомпозите» из ПКМ могут сделать элероны, спойлеры, закрылки, рули высоты и направления, лонжероны и обшивку крыла со стрингерами, секции панелей центроплана, силовые элементы, обшивку киля и хвостового оперения.
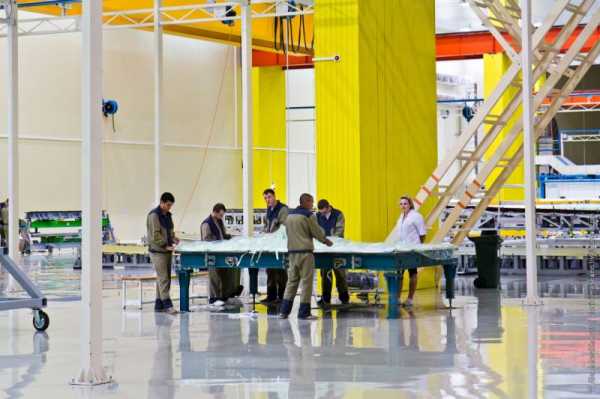
4. Вот так выглядит оснастка для выкладки одной из деталей силовой конструкции МС-21:
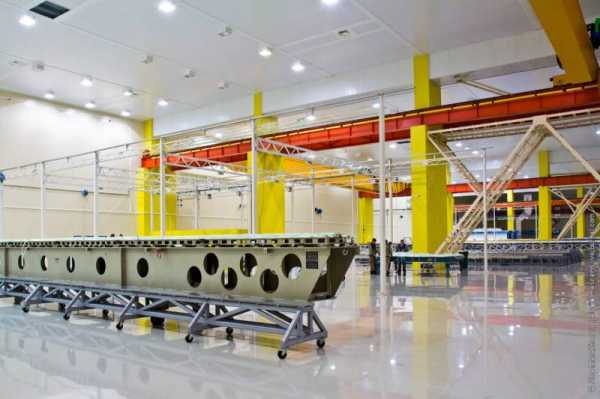
5. Тяжёлые конструкции оснастки транспортируются к месту выкладки на специальных платформах. К примеру, для перевозки оснастки для будущего стрингера задействуют две таких тележки.
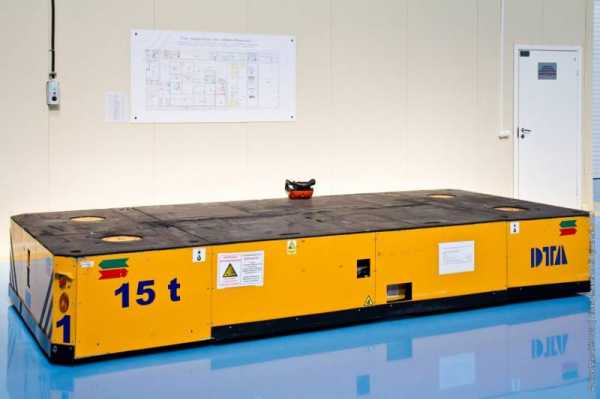
6. Следующий этап — выкладка сухой углеродной ленты и предварительное формование детали в автоматическом режиме на выкладочной оснастке. Для выкладки используется роботизированный испанский комплекс MTorres.
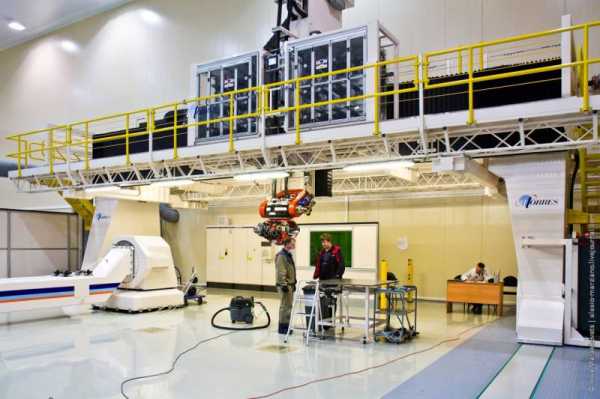
7. Он немного напоминает GLaDOS из компьютерных игр Portal и Portal 2.
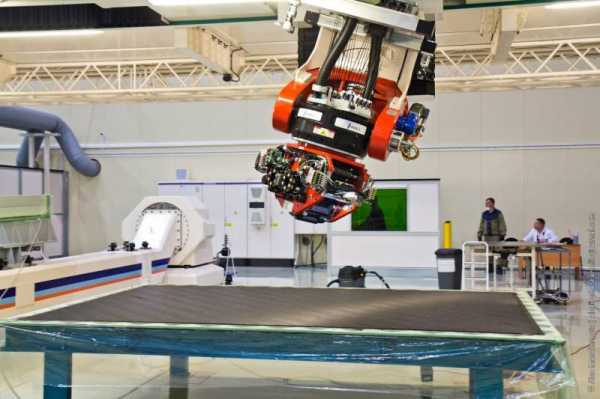
8. Этот робот с высокой точностью укладывает волокно к волокну, формируя слои будущей конструкции.
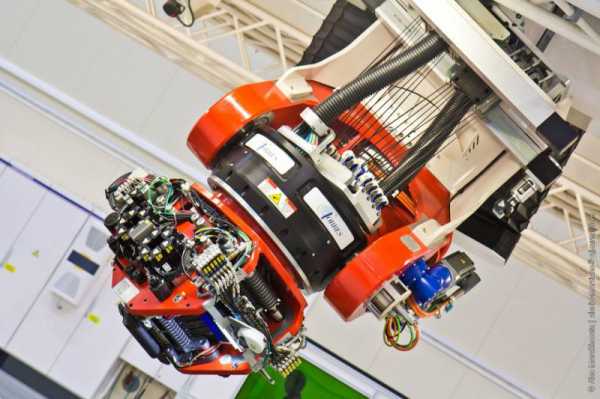
9. Автоматическую выкладку сухого углеволокна для изготовления крупных интегральных конструкций никто никогда в авиапромышленности не применял. Такое крупное и сложное изделие, как крыло самолёта, по этой технологии впервые сделали в Ульяновске.
Собранная преформа уезжает в термоинфузионную установку TIAC (Франция). Это большая камера, в которой углеволокно пропитывается эпоксидной смолой и запекается. Установка контролирует температуру, количество смолы и скорость заполнения вакуумного мешка, в который помещается углеволокно.
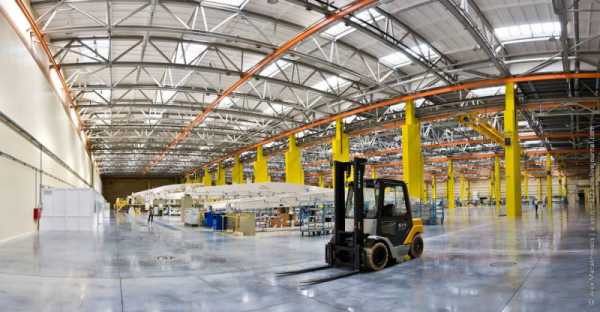
10. Этот процесс может занимать от 5 до 30 часов в зависимости от типа, размера и сложности изготавливаемой детали. Процесс полимеризации смолы и волокна проходит при температуре 180°С.
На выходе из TIAC получается монолитная деталь.
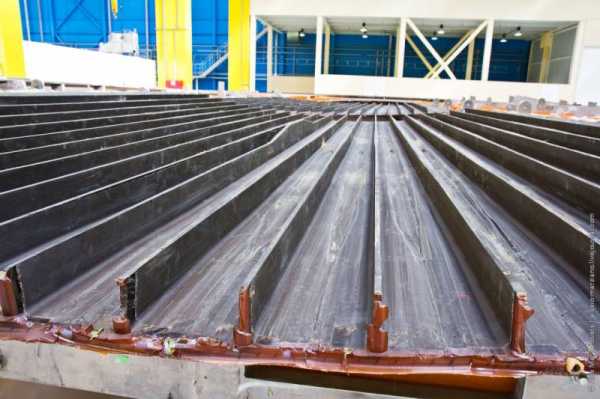
11. Её необходимо механически обработать.
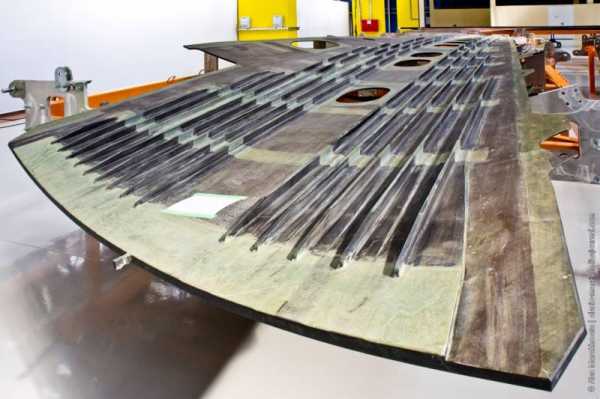
12. Но до начала обработки нужно убедиться, что деталь действительно является монолитной и не содержит в себе пустоты и дефекты. Для этого она отправляется на пункт неразрушающего ультразвукового контроля Technatom.
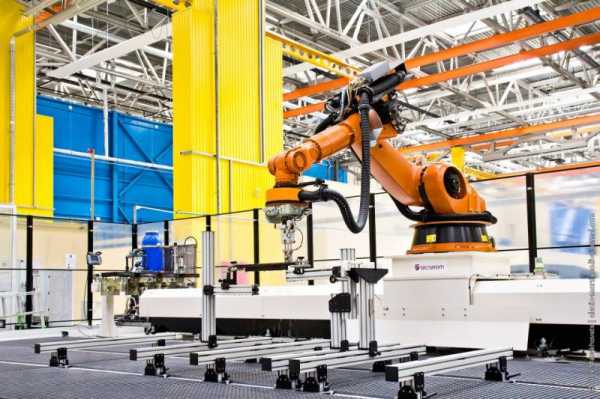
13. Крыло получилось качественным — отправляем его на механическую обработку в 5-координатный фрезерный центр MTorres.
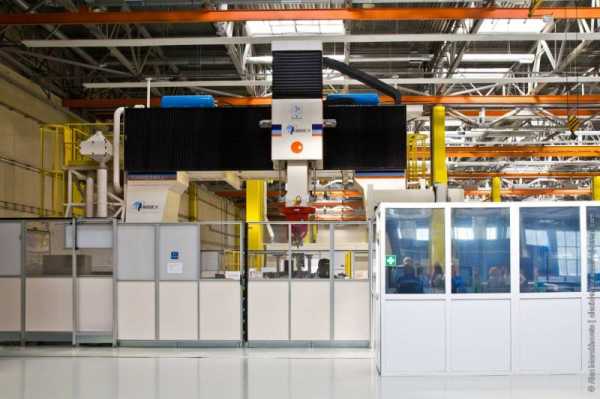
14.
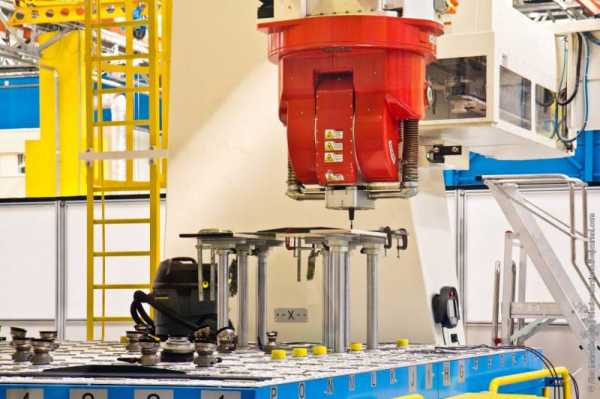
15.
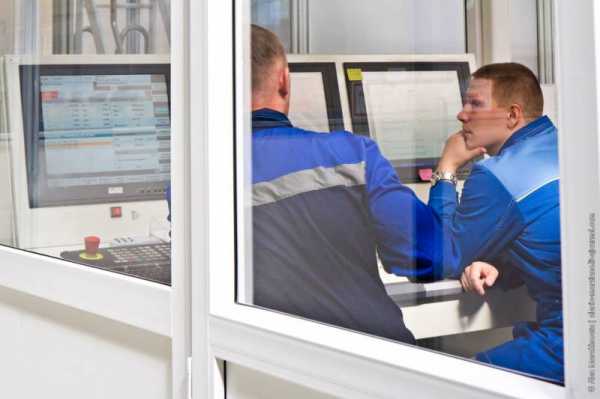
16. После обработки готовая деталь поступает на участок итоговой сборки кессона крыла.
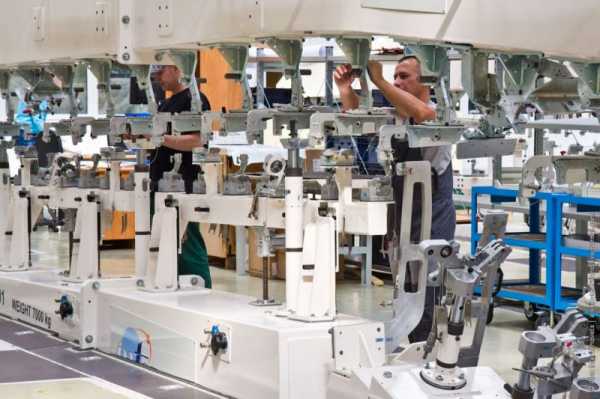
17. В этой части завода используется больше ручной труд, чем автоматический. Здесь гораздо больше людей, тогда как на других участках их почти нет — вся работа выполняется роботами. А всего на заводе работает около 500 человек. Несмотря на постоянно открытые вакансии, устроиться сюда не очень просто — каждый кандидат проходит тщательную проверку.
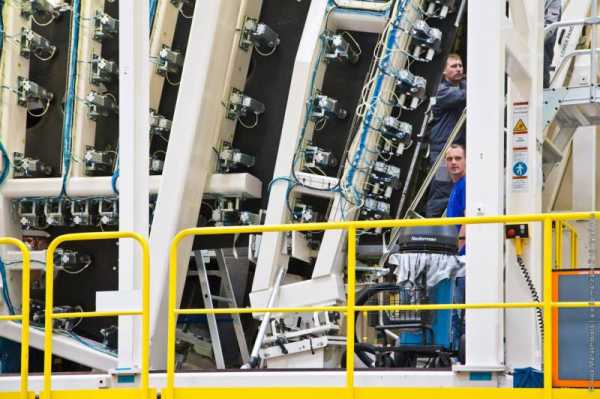
Летаем на композите
18. Композитные крылья будут использоваться не только на МС-21. Планируется, что новые модификации SSJ-100 так же будут оснащаться силовыми деталями из ПКМ. Мощности завода рассчитаны на выпуск до 100 комплектов композитных крыльев в год, но на текущий момент загружены не полностью.
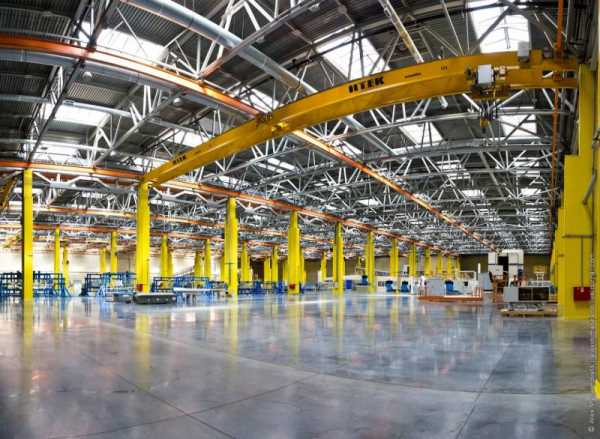
topwar.ru
Сборка крыла классической конструкции — DISCOVERY AEROMODELS
1.Бальзовое крыло классической конструкции.
Основные требования:
-Достаточно прочное
-Жесткое на изгиб и кручение
-ровное
В модели летит и несет крыло. Главный элемент, определяющий полет модели. Отнеситесь предельно серьезно к изготовлению. Речь не будет идти о профиле, оставим это для отдельной темы, говорим только о конструкции и технологии.
а)
Для сборки ровного крыла нужна ровная базовая поверхность. Если нет, придется создать. Как- зависит от ваших возможностей. Но без этого вероятность успеха призрачна. Чем ровнее поверхность (стол), тем лучше.
б)
Для сборки крыла используются 2 ровные стапельные планки с карнизом для установки нервюр.
Ровные- значит ровные максимально, как линейка, а не условно ровные, «на глаз». От этого зависит, насколько ровным будет Ваше крыло. Высота планок каждой в отдельности вдоль длины должна быть одинакова. Насколько позволяет точность Вашего мерительного инструмента и представления об отклонениях, которые Вы допускаете для крыла. Сделайте эти планки. Оклейте тонким пластиком, чтоб не повелись со временем, если планки из дерева. Водорастворимый клей не применяйте. Как и мокрое дерево, понятно.
Склейку производить на ровной поверхности, без деформаций и напряжений. Например, если планка кривая, не надо пытаться сделать ее ровной методом загрузки тяжестями при склейке, все равно эти напряжения «вылезут» деформациями позже. На оснастке не экономят, сделайте разумно. Иначе будете делать кривые крылья и удивляться, почему же все модели летят одинаково криво? То же относится к прямолинейности лонжеронов.
Будьте внимательны вдвойне к круткам, так как если к примеру Ваше приспособление обеспечивает крутку консоли на 0,5 мм
(подумаешь, пол миллиметра…), то собранная на этом же приспособлении другая консоль будет закручена в ту же сторону на те же пол- миллиметра. В совокупности, общая крутка крыла, составленного из этих 2-х консолей, составит 1 мм, что весьма много, поверьте.
в)
Согласно контуру профиля, изготовьте болванку для гибки бальзового «лобика» крыла.
От наружного контура отнимите
толщину бальзовой обшивки, создайте шаблоны и строгайте. Можно на ЧПУ. У кого
есть возможность. Рекомендуемая толщина
обшивки 1,5- 2,5 мм,
в зависимости от плотности бальзы и желаемых веса крыла и устойчивости
межнервюрных пролетов. При тонкой легкой бальзе после обтяжки межнервюрные
прогибы лобика заметнее. Но он легче. Выбирайте, что Вам важнее. В любом случае.
Вы вынуждены искать
компромисс.
г)
Теперь сделайте шаблоны
нервюр из металла или фанеры.
Они должны быть абсолютно
симметричны.
Несимметричный шаблон произведёт несимметричные нервюры и профиль крыла.
Несимметрия профиля это аэродинамическая крутка. Причем на разных консолях,
выполненным по одним несимметричным
шаблонам, крутка удвоится. Будьте аккуратны, избегайте разочарований и
экономьте время в итоге.
Соберите на ровных штырях диам. 3- 4 мм пачку нервюр, обработайте. Приклейте в точках сборочные планки к столу. Установите нервюры по разметке. Нервюры должны быть пронумерованы и установлены в порядке нумерации.
д)
Дальше просто сборка. Приклейте лонжерон к нервюрам. (Рис. 1).
Лонжерон не должен выступать или западать за контур нервюр. Все вровень. Наложите на носовую часть нервюр гнутый бальзовый лобик,
убедитесь что он лежит без зазора на полке приспособления, проходит через средину лонжерона и хорошо прилегает к нервюрам. Подгоните при необходимости. (Рис. 2)
Не оставляйте вышкуривание лобика на собранном крыле, лучше это сделать до сборки на болванке, иначе получите провалы поверхности в районе нервюр.
Клеить можно и эпоксидной смолой, и ПВА, и другими крепкими клеями. Если клей сохнет долго, надо обеспечить прилегание лобика к нервюрам в течение всего времени высыхания. Зазор между лобиком и нервюрой — это искривление профиля со всеми вытекающими последствиями. Прижать лобик можно грузами и булавками. Не приклейте лобик и нервюры к планкам стапеля.
При достаточном навыке и
сноровке можно клеить быстросохнущими клеями — суперклеем (цианоакрилатом). Но
это высший пилотаж.
е)
Приклейте полку задней кромки шириной 20-40мм. Нарежьте полки нервюр (тавровки, по другому) шириной 10 мм
и приклейте к нервюрам, лонжеронам и полке задней кромки, подгоняя каждую по длине. Зашейте полностью 3 нервюры центроплана бальзой.
Верхняя половина готова.
ж)
Осторожно вынимаете конструкцию из стапеля, переворачиваете и вставляете в стапель вновь. Повторяете все для обратной стороны.
Дальше установите стенку лонжерона. Слоя бальзы- вертикально.(Рис. 3).
Стенка лонжерона замыкает лобик в замкнутый контур, обеспечивающий жесткость крыла на кручение. Не установив стенку Вы получите слабое на кручение крыло, это непременно скажется на управляемости.
З)
Можно сделать жесткую обшивку
крыла. Зашив все крыло бальзой, вместо тавровки. Получится немного тяжелее, но
намного жестче и прочнее. При этом можно уменьшить сечение лонжерона. Еще, для
экономии веса, полки лонжерона делают переменного сечения, уменьшая его к
законцовке .
Нагрузка на лоржерон уменьшается в этом направлении
пропорционально.
В заключение стапельной сборки сделайте и вклейте бальзовые бобышки (бонки) навески закрылка, чаще 3 или 4 шт. на консоль. Вклеивая их между полками задней кромки, не разоприте их. Если у вас жесткая обшивка крыла, бобышки придется вклеить перед приклейкой обшивки второй половины, т.к. обшивка закроет доступ к вклейке бобышек.
и)
Вынимаете консоль из стапеля. Для завершения сборки надо заклеить щель в передней кромке крыла и приклеить торцевую часть задней кромки. Делается это на стапельных стойках, чтобы не нарушить плоскостность крыла.
Стапельные стойки удерживают консоль от крутки. Но не нагружайте
консоль изгибающими нагрузками при работе, чтоб не получить прогиб. (Рис. 4).
discovery-aeromodels.com
Изготовление матриц для передних крыльев
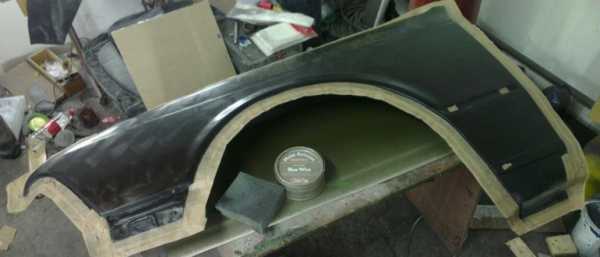
На данный момент все популярнее становится тюнинг и облегчение кузова автомобиля. Так же если вы обладаете достаточно старым автомобилем, то некоторые фрагменты кузова очень сложно достать, или же они будут стоить просто баснословные суммы денег. На первый взгляд, это является очень затратной частью, но ничего страшного в этом нет, ведь вы всегда можете сделать не большой custom своими руками.
Мы расскажем с помощью чего, можно сделать при минимальных затратах новые передние крылья не уступающие по прочности заводским аналогам.
С чего же начать?
- Первым этапом в постройке матрицы передних крыльев является выведение первоначальной формы крыла. Если есть неровности, вмятины, проржавевшие места, все это необходимо выровнять, за шпаклевать, и вышкурить, добиться максимального эффекта к заводским параметрам.
- Обклеиваем окантовку металлическим скотчем или плотным картоном
- Наносим втирая на нашу поверхность воск с помощью губки (данный этап проводится в 3-4 слоя с промежутком высыхания 1 час)
- После высыхания последнего слоя накладываем матричный гелькоут(наносится в 2 слоя с промежутком 20-25 минут. После чего необходимо отстоятся 4 часа для полного высыхания)
- Наносим слой стекловуали(тщательно укладываем и промазываем все неровности,впадины и изгибы что бы не образовалось пористого места)
- Наносим 2 слоя стекломата 300 с промежутком слоя 1 час и затем 600 с промежутком слоя 1 час. Даем высохнуть 5-6 часов.
- Что бы предать матрице более плотную форму и избежать деформации или поломки самой матрицы, необходимо сделать каркас жесткости. Для использования каркаса можно использовать деревянные доски
- Подгоняем доски под наше крыло,скручиваем саморезами для прочности и заливаем несколькими слоями с промежутком 1 час стекломат 600
После чего даем пару дней полностью высохнуть изделию. - После высыхания, обрезаем лишние края и аккуратно извлекаем деталь из матрицы.
Матрица передних крыльев готова
Источник: DRIVE2
Понравилась статья? Поделить с друзьями:
avtosovet.info
Как быстро собрать крыло rc авиамодели своими руками
Один из важных этапов постройки авиамодели – сборка крыльев. Чтобы крыло полностью оправдало себя и не подвело вас в полёте, нужно правильно собрать основные его узлы: лонжероны и нервюры. Также правильно приклеить обшивку, закрепить переднюю и заднюю кромки. Задач не так много, но от результата вашей работы зависит то, насколько долго ваш самолёт будет радовать вас и ваших близких. Изобретать велосипед умеет каждый, а вот перестать заниматься лишней работой можно, если обратиться к чужому опыту.
Сборка лонжерона и несиловых нервюр
Начать собирать крыло можно с полки лонжерона и с несиловых нервюр. Чтобы процесс не был таким утомительным, первым делом распечатайте эскизы крыла с помощью Автокада. На вашем чертеже должен быть виден профиль лонжерона, передняя и задняя кромки крыла, а также расположение каждой нервюры (ребра жесткости крыла). Самое главное в чертеже – отображать реальные размеры между деталями. Без такого эскиза в масштабе 1:1 сложно будет ожидать высокой производительности и удовольствия от работы.
Эскизы крыла создаются в Автокаде. Для того чтобы профиль крыла себя оправдал, при проектировании учитывается всё: вес, устойчивость планера в полёте, а также балансировка авиамодели. Более подробно процесс проектирования освещен в статье: проектирование.
Сборка начинается с расположения верхней полки лонжерона на чертеже крыльев в масштабе 1:1. Из-за конструкции крыла лонжерон необходимо подпереть несколькими опорами. В качестве опор подойдут деревянные бруски, либо металлические втулки одного диаметра. Особое внимание следует обратить на отсутствие прогибов в центре и по бокам.
Сборка крыла начинается с концевого ребра жесткости. При этом нужно учитывать угол кручения крыла. Для этого нервюры устанавливаются в пазах лонжерона под определенным углом. После того как вы установите горизонталь с помощью двух угольников, следует приступать к посадке ребра на клей.
Нанесите древесный клей на паз концевого ребра жесткости. Затем снова сориентируйте его относительно линии стола с помощью угольника. Для этого совместите заднюю кромку и отметку на передней кромке так, чтобы эти две точки находились на одной высоте от линии стола. В случае на фотографии это выравнивание даст угол атаки в 2 градуса, как было задумано. Как только подъём нервюр будет обеспечен, следует убедиться, что плоскости нервюр совпадают с желаемым положением и с чертежом.
Ту же самую процедуру стоит повторить для корневого ребра жесткости.
Теперь у нас есть два крайних ребра жесткости, посаженные на клей. Благодаря этому мы сможем размещать оставшиеся нервюры под нужным углом кручения без надобности замера их высот над поверхностью стола.
Когда все нервюры стоят на месте, передвигайтесь к концу крыла и смотрите сверху вниз вдоль плоскости крыла. Важно, что задняя кромка концевого ребра совпала с задней кромкой корневого ребра.
Теперь отрегулируйте нервюры, которые вы выставляли, так, чтобы задние кромки между двумя ближайшими нервюрами также совпали.
При регулировке нервюр стоит периодически сверять их положение с чертежом и правильным положением относительно линии между задними кромками от концевого до корневого ребра. После выставления используйте клей.
Повторяем эту же процедуру для другого крыла.
Установка центральных и посадочных нервюр
После несиловых очередь доходит до посадочных нервюр. Для их склеивания не подойдет обычный клей ПВА. Поскольку он сделан на водной основе, которая плохо проникает в смолу и не создаёт с ней прочного соединения. Поэтому для склеивания подходят только специальные марки клеев: полиэфирные или эпоксидные.
Перед тем как приступать к сборке, нужно проверить посадку нервюр на лонжерон. Лучше, если эта посадка будет тугой, тогда можно подработать рашпилем. Хуже, если посадка просаженная, в этом случае, можно использовать прокладки или эпоксидную смолу.
После обеспечения нормальной посадки не забываем про защиту рук и органов дыхания от вредных испарений эпоксидного клея.
Пяти минутный эпоксидный клей подойдет для проведения процедуры лучше всего. После его перемешивания закапываем по несколько капель в каждое сопряжение.
Процедура установки центральной нервюры не отличается от установки несилового ребра. Сначала мы выставляем угол атаки с помощью двух угольников, а уже потом наносим эпоксидный состав.
Установка посадочных ребер не отличается в корне от установки центральных ребер с небольшим исключением.
Для свободного выпуска шасси на нервюрах нужно предусмотреть прорези. Из-за двугранного угла крыла при открытии шасси могут загнуться в наружную сторону. Чтобы этого избежать их нужно размещать под небольшим углом в посадочных нервюрах. Для этой авиамодели данное значение не превышает 1,5 мм. После установки правильного положения нервюр и шасси, их можно сажать на клей.
Установка нижней полки лонжерона
Установка нижней полки лонжерона может оказаться не простым занятием, поскольку он должен входить в пазы всех нервюр при тугих посадках. Во время этой сборки всплывают все погрешности взаимного расположения нервюр относительно друг друга и погрешности обработки пазов. Кроме того, сама полка состоит из двух склеенных реек и собирается в последнюю очередь.
Для сборки крыла убедитесь, что крыло все ещё поддерживается на весу и не провисает в центре или вдоль размаха крыла. Возможный провис можно устранить с помощью установки дополнительных опор.
Попробуйте установить одну половину верхней полки лонжерона. При этом нужно оставить слабину полки лонжерона по центру для легкости его соединения с другой половиной. Установка лонжерона в пазы нервюр должна происходить достаточно легко. Если это не так, то тесные пазы расширяются с помощью наждачной бумаги, слишком свободные пазы укрепляются прокладками. Нельзя допускать не достаточно плотной посадки полки в паз – всё отобразится на обшивке.
Наиболее сложный этап при установке лонжерона – это клейка. Склеивать лонжерон необходимо одновременно во всех пазах. Следовательно, необходим творческий подход для решения задачи удержания лонжерона в пазах и его склейки. Для фиксации деталей на время застывания клея, я использовал изоленту и малярный скотч.
На следующем этапе сборки устанавливается вторая половина полки. Кроме правильной посадки второй половины во все пазы, важно также чтобы обе половинки плотно сопрягались друг с другом. Данное условие является прямым следствием из-за нагрузок, возникающих в этом соединении во время полёта.
В дополнение к проверке и регулировке посадки полок лонжерона, также нужно отрегулировать их взаимное положение относительно друг друга.
Как только взаимное положение отрегулировано, фиксируем его с помощью изоленты и малярного скотча.
Для склеивания частей полки используется эпоксидная смола, при этом не надо забывать про фиксацию всех соединений.
После склейки двух половинок полки лонжерона происходит окончательная клейка второй половины полки лонжерона в пазах нервюр.
Монтаж передней кромки крыла
Передняя кромка крыла – это брусок бальзы толщиной 0,6 см, который присоединяется к ребрам жесткости крыла спереди. Он служит для жесткости крыла, а также для крепления обшивки на крыльях, поскольку обшивка вокруг крыльев не гнется. Второе его назначения в том, чтобы обеспечить достаточную толщину передней кромки для её ошкуривания по форме аэродинамического профиля.
Перед установкой обшивки ошкурите законцовки ребер очень аккуратно с помощью шлифовального бруска. Важно, чтобы у всех ребер были одинаковые углы, и все они были идеально ровными.
Вырежьте полосы из пробкового листа, толщиной 0,6 см. Чтобы облегчить разрезание длинных полосок материала используйте двухсторонний скотч, для чего прилепите заготовку к длинной доске на скотч и обрабатывайте заготовку прямо на доске. Также не стоит пытаться разрезать заготовку за одни проход, поскольку можно её расщепить. Вместо этого отрезайте полоску за несколько раз.
Полоски должны соответствовать передней кромке.
Используйте циакриновый клей для приклеивания кромки к ребрам жесткости. Легче всего сначала приклеить полоску к концевой нервюре, а затем выровнять её по центральному ребру. Как только клей схватился, переходите к склеиванию следующих нервюр и так далее. Будьте осторожны, не повредите соединения, которые уже были заклеены.
Клейте до тех пор, пока не заклеите полностью одну из сторон крыла.
Отрежьте лишнее, а затем ошкурите переднюю кромку, пока она не будет соответствовать чертежному контуру.
Приклейте переднюю кромку на крыло, как было показано до этого. Убедитесь, что оно зафиксировано, как на фотографии.
После приклеивания кромок с обеих сторон их контуры должны совпасть. Место сопряжения двух частей передней кромки склеивается в последний момент.
После склеивания можно приступать к ошкуриванию. Для этого наклейте полоску изоленты сверху ребер жесткости, которые будут ошкуриваться. Это защитит ребра и послужит направляющей для шкурки.
Для улучшения качества обработки кромок можно пользоваться тонкой изолентой.
После присоединения передней кромки начните её обрабатывать с помощью шлифовального бруска с наждачной шкуркой или маленького рубанка. Кромка не должна быть круглой спереди, скорее она должна быть трапецеидальной.
Помните, что ребра обрабатывать не нужно. Для их защиты служит как раз изолента.
С помощью шлифовального бруска ошкурите переднюю кромку в соответствие с контуром. Качество крепежа нервюр можно частично проконтролировать по звуку. Стук ребер при шлифовке говорит о плохой проклейке.
Монтаж пояса лонжерона
Продольный набор крыла состоит из бальзовой фанеры толщиной 0,8 мм, приклеенной к верхней и нижней полке лонжерону, а также к крыльевым нервюрам. Важно, чтобы пояс между нервюрами сидел туго, потому что в противном случае нагрузки на крыло его повредят. В таком случае лонжерон будет работать как I – образный профиль, а не как несколько полосок.
Вырежьте листы из бальзовой фанеры размерами чуть больше, чем промежуток между лонжеронами и нервюрами.
Ошкурите каждую поперечину до тех пор, пока она не будет жестко входит в пространство между двумя ближайшими нервюрами.
Приклейте поперечины к верхнему и нижнему поясу лонжерону с помощью циакринового клея.
![]() Каркас крыла | ![]() Каркас крыла, вид 2 |
Обшивка верхней плоскости крыла
Вся обшивка на этой модели выполнена из 0,8 мм бальзовой фанеры. Внешний вид модели можно оставить без покраски, естественный цвет фанеры будет выглядеть очень эстетично. Но не зависимо от того, красите вы или нет, вам нужно позаботиться об однородности цвета обшивки. С этой же целью важно сделать все швы как можно более ровными и гладкими, чтобы древесный наполнитель не высвечивался после финишной сборки.
Выберите листы бальзы, которые будут крепиться к кромке крыла. Важным моментом является контур крыла, структура кромки, цвет и твердость кромки.
Если два соединяемых листа обшивки плохо подходят друг для друга, например, кромки не совпадают или волнистые сами по себе, то для их сопряжения по прямой можно использовать длинный шлифовальный брусок.
Приготовьте вощеную бумагу и положите её на стол.
Возьмите лист упаковочной ленты и положите его сверху на вощену
1aviaclub.ru
Изготовление крыла мотоцикла с нуля с чистого листа
Крыло мотоцикла с чистого листа.
Перед начинающими кастомайзерами при изготовлении чоппера, часто встаёт вопрос: где взять навеску для своего мотоцикла? А ещё чаще возникает вопрос: как её изготовить самому? И начинаются, как обычно, переделки из заводских мотоциклетных деталей. Режутся на куски стандартные баки, крылья, бардачки, и начинается добавление кусков металла и как всегда используется ведро шпаклёвки. В итоге эти детали обычно получаются чуть ли не в двое тяжелее оригинала, а вес, особенно для крыла, играет важную роль, так как при компоновке крыла с минимальным зазором от колеса получается прикольный вид, но в таком случае крыло нужно крепить уже не к раме, а к маятнику. И вот при таком креплении, тяжёлое крыло увеличивает неподрессоренную массу, что не лучшим образом сказывается на движении байка.
Можно конечно сделать деталь из стеклопластика, но если попробовать работать с ним, то оказывается возни с ним намного больше, чем с листовым металлом (проверено). При изготовлении обычного крыла из листового металла (не очень глубокого), у меня затрачивается времени меньше одного дня, и можно его красить, а при изготовлении такой же детали из стеклопластика, только на изготовление матрицы уйдёт намного больше времени, потом уже идёт изготовление детали, и плюс сутки на просушку. Ну и затем сколько возни на зашкуривание и шпаклёвку я лучше умолчу. А вес стеклопластиковой детали, практически такой же, как и у стальной, потому что при уменьшении веса (толщины пластика), крыло становится очень хлипким. Ну и для чоппера пластиковые детали, сами понимаете — не в тему.
Ещё один большой минус таких переделок — одинаковость, это главная беда многих отечественных кастомов. Куда ни глянешь, везде видны фрагменты отечественных жестяных деталей, основная доработка которых, это расширение размера. Оно и понятно — многих останавливает недостаток информации и инструмента по работе с листовым металлом. В этой статье я постараюсь этот недостаток исправить, но опять же напомню, что описываться будет самое простое крыло, чтобы вам было легче понять технологию работы. Изготовив простое крыло для чоппера, в дальнейшем сделать крыло более глубокое или сложное по дизайну, вам не составит труда, так как поняв технологию и принцип работы, без проблем можно перейти от простого к сложному.
Я думаю хватит философии, пора заняться делом. Как обычно на любом заводе, изготовление качественной детали начинается с чистого листа бумаги. Так и мы, начинаем с чистого листа, а точнее картона. Вырезаем полоску картона длинной на ваше усмотрение. То есть вырезав полоску чуть длиннее чем нужно, примеряем к мотоциклу над колесом, и определившись с нужной длинной, отрезаем лишнее. А вот с шириной отпишусь немного поточнее. Для покрышки шириной 130 мм, ширина полоски картона должна быть на 40 мм шире и это для неглубокого крыла (какое вы видите на нижних фото). Значит нетрудно подсчитать ширину полоски для покрышки шириной аж на 360 мм: 360 + 40 = 400 мм. При обработке металл немного вытянется, но уверяю, не на много, к тому же немного ширины заберёт радиус загиба по контуру покрышки. Если вы хотите более глубокое крыло, тогда ширину полоски нужно увеличить на пару сантиметров, а можно и больше, ведь лишнее всегда можно отрезать. При изготовлении более глубокого крыла, металл вытянется чуть больше, и это надо учесть, хотя опять повторюсь — лишнее всегда можно отрезать.
Определившись с размерами картонного шаблона крыла и перепроверив его на мотоцикле, закругляем (подрезаем) края полоски спереди и сзади (можно края подрезать более оригинально, чем на фото, я напомню это базовые знания) и переносим размер на миллиметровый лист металла (накладываем и обводим маркером). Затем вырезаем из листа металла нужную деталь болгаркой, ножницами, или электро-лобзиком, и заглаживаем кромки детали напильником или шлифовальным диском, убирая заусенцы.
Дальнейшая работа предстоит самая интересная: придание объёма плоской детали. Для этого потребуются: кожаная подушка, набитая песком или дробью (можно использовать дубовый пенёк с углублением в центре), и два самодельных молотка, со сферическими бойками. Один из них обычный (красный на фото) для начальной выколотки металла, а второй (чёрный на фото) понадобится для выколотки, когда крыло станет глубоким, и кромки его начнут упираться в ручку обычного молотка и мешать работе. Эти молотки я изготовил из шаровых опор грузовика ( у шаровых опор сталь качественная), а самый большой шар (сферу) на чёрном молотке, пришлось заказать токарю выточить из твёрдой стали. Сферические бойки молотков нужно обязательно отполировать до зеркального блеска.
Уложив металлическую листовую заготовку крыла на кожаную подушку, начинаем наносить частые равномерные удары сначала по центру листа, и плавно переходим к краям. При ударах лист будет стремиться свернуться вовнутрь, и это неплохо, так как нужно будет всё равно согнуть крыло по радиусу колеса, но при сильном сворачивании, деталь постоянно распрямляем и подправляем руками.
При выколачивании проверяем плавность закругления крыла (при виде спереди), а то может получиться так, что в центре радиуса закругления, крыло будет более выпуклым (острым), чем на краях. Значит нужно будет пройтись молотком ближе к кромкам по всей длине крыла, чтобы в итоге получить плавный радиус при виде спереди и сзади.
При выколачивании вы увидите, что постепенно глубина крыла увеличивается и здесь нужен другой молоток, так как кромки начинают упираться в ручку молотка и не дают нормально ударить. Нужно поменять молоток на другой (черный на фото) изготовленный с отдалённой рукоятью от сферического бойка.
Прикладывая деревянный шаблон, проверяем одинаковость выпуклости по всей длине.
Начинающим кастомайзерам, которые имеют небольшой опыт работ с листовым металлом, бывает трудно добиться одинакового профиля (выпуклости) крыла по всей длине. Таким людям я советую пользоваться деревянным шаблончиком из дерева (смотрите фото слева), прикладывая который по всей длине крыла, вы сможете проверять одинаковость выпуклости по всей длине.
Что касается радиуса крыла при виде сбоку (то есть радиуса самого колеса) то тут всё немного сложнее. При выколачивании металла, в середине крыла появляется выпуклость и металл растягивается, но с боков (ближе к кромкам) мы удары не наносим и металл остаётся каким был — более толстым, чем в середине. К тому же при получении объёма (выпуклости) крыло становится довольно жёстким и радиус его становится намного больше радиуса колеса. Согнуть его, для уменьшения радиуса (чтобы подогнать радиус к колесу) становится не так то просто и при загибе на кромках появляются некрасивые волны. Это создает небольшие трудности при работе.
Для облегчения процесса и придания нормальной формы крылу (без волн на боковинах крыла) нужно листовой металл на боковинах крыла сжать, то есть сделать металл на боковинах (кромках) крыла ещё толще. Для этих целей обычно применяют шринкель, но он есть далеко не у всех. Я предлагаю более древний и простой вариант, которым пользовались ещё при изготовлении рыцарских доспехов. Нужно по всей длине обоих боковин выдавить гофры (см. фото) и при их выдавливании вы увидите, что крыло само начинает уменьшать свой радиус. Гофры нужно выдавить так, чтобы радиус крыла стал намного меньше радиуса колеса (если диаметр колеса на 16 дюймов, а радиус естественно 8 дюймов, то диаметр крыла с гофрами должен получиться примерно на 12 дюймов, а радиус соответственно всего 6) и далее объясню для чего это нужно.
Дело в том, что теперь, чтобы сжать (сделать металл толще) боковины крыла, нужно эти гофры выровнять ударами молотка или специальной лопатки (см. фото). Нанося удары на гофры на выпуклой наковаленке, мы одновременно и выравниваем боковины от уже ненужных гофров, и одновременно сжимаем и утолщаем листовой металл, так как при выравнивании гофров, от ударов идёт наволакивание металла и его одновременное сжатие по длине и утолщение листа по толщине — так называемый наклёп металла. Но при этом процессе опять идёт увеличение радиуса крыла (крыло постепенно выпрямляется), и именно для этого я и написал выше, для чего нужно сделать радиус крыла с помощью гофрирования намного меньше, чем радиус колеса.
В итоге нужно добиться, чтобы радиус крыла совпал с радиусом колеса (при работе крыло постоянно прикладываем к колесу), и процесс гофрирования и обстукивания (выравнивания и наклёпа) боковин иногда приходится сделать пару раз, а на более глубоком крыле бывает и три-четыре раза.
Но это довольно быстрый процесс, если сделать специальную гофрилку из любого небольшого прессика (см, фото и видео чуть ниже). Если нет пресса или нет времени возиться (я потратил на изготовление всего день), то можно сделать простую гофрилку из двух штырей (прутков) диаметром 8 — 10 мм, приваренных рядом друг с другом на расстоянии пару мм (типа вилки).
Про шринкер и стретчер желающие могут почитать вот в этой статье.
С этим устройством работа пойдёт немного медленнее, так как чтобы сделать одну волну (гофру), придётся поместить кромку крыла между штырей и затем провернуть крыло между ними и отодвинув его дальше (по длине) примерно на сантиметр опять провернуть. Но работать вполне возможно и привыкнув можно увеличить скорость гибки.
При желании можно сделать более глубокое крыло (см. фото справа), если ещё раз пройтись по всему крылу частыми ударами, но тогда общая ширина крыла может уменьшится и крыло станет глубже но тоньше по ширине.
После нанесения гофров, их выравнивания и подгонки радиуса закругления крыла к радиусу колеса (об правильном изготовлении самодельного мотоциклетного колеса, но с заводской технологией, можно почитать вот здесь), всё равно могут остаться небольшие волны на кромках крыла, но это уже мелочи и исправляются они обстукиванием на выпуклой наковаленке. Обстукивать можно плоской лопаткой или молотком с плоским полированным бойком, и при работе иногда можно подровнять волны на металле кромки, нанося удары и с внутренней стороны крыла.
Подровняв по кругу кромки крыла, переворачиваем крыло выпуклой стороной вниз, и уложив его на плоскую гладко-шлифованную наковальню (фото её можно увидеть в этой статье про изготовление бака), обстукиваем изнутри всё крыло пластиковой киянкой, с сферической поверхностью ударной части. Это нужно, чтобы немного подровнять шишки на металле, и ускорить прокатку на английском колесе. Впрочем у кого мощное и большое английское колесо, и есть опыт работы с этим станком, то операцию обстукивания на плоской наковальне можно не применять.
Остаётся одна из самых интересных операций — прокатка крыла между роликами английского колеса, и превращение мятого и невзрачного куска металла в гладкое и привлекательное изделие, для которого перед покраской не требуется ни грамма шпаклёвки. Процесс прокатки описывать не буду так как он не сложен и начав прокатывать деталь, научится можно через пару часов тренировки. К тому же немного об этом я написал в статьях про бензобаки. И уверяю вас, что работая на этом станке, вы с каждым днём и довольно быстро будете открывать новые, более удобные для вас методы работы без всяких подсказок. Это станок который надо почувствовать и советы здесь бессмысленны. Скажу только одно — на первых порах работы, держите пальцы подальше от роликов, так как усилие от скобы может составлять несколько тонн.
После прокатки крыла на английском колесе, можно ещё раз подравнять волны на кромках крыла (если они есть), обстукиванием на выпуклой наковаленке по периметру всего крыла, а можно чуть загнуть кромку, по периметру нанося более сильные удары и держа кромку немного под углом к наковальне. Это сделает крыло жёстче. При необходимости, кромки можно снова прокатать на колесе. Кстати о жёсткости: кому посчастливилось изготовить или купить станочек, называемый зиговочная машинка, то подобрав в продаже или выточив на станке специальные ролики, можно завернуть кромку крыла во внутрь, прокатав между роликами всё крыло по периметру. Это придаст изделию красивый законченный вид и дополнительную жёсткость. О зиг-машинке можно почитать здесь, но у кого её нет, можно аккуратно приварить по периметру кромки крыла проволоку (изнутри), диаметром 4 — 5 мм, тем самым добавив жёсткость крылу и более достойный вид.
Способов креплений крыла множество. Можно приварить аккуратные ушки с отверстиями к крылу и к ним добавить стойки, а можно аккуратно просверлить отверстия в крыле, а к отверстиям прикрепить стойки с помощью заклёпок или болтов. Есть неплохой способ крепления крыла когда стойки, держащие крыло, выполнены из крученного квадратного прутка и продолжаются вверх, образуя спинку — сисибар. Этот вариант часто используется в шведской школе кастомайзинга. Несомненно выбирать вам, и большая возможность выбора является одним из главных приколов кастомайзинга.
Тем мастерам, для которых на первом этапе тяжело приобрести или изготовить станок английское колесо, посоветую изготовить крыло для мотоцикла без использования английского колеса. Как это осуществить, можно узнать кликнув вот по этой ссылке.
И последнее. Чтобы заказать крыло для кастома из каталога, придётся выложить около 300 долларов, а за крыло для покрышки на 360 мм — ещё больше. Но при самостоятельном изготовлении, вы потратите за кусок листового металла цену около 1 доллара и получите кучу положительных эмоций. Как говорилось в какой то рекламе — почувствуйте разницу. Но не это главное: изготовив крыло для мотоцикла своими руками, вы получите изделие в единственном экземпляре и что самое главное — гордость за себя, а это поверьте дороже денег. Успехов всем!
suvorov-castom.ru
Деревянные навесы: технология изготовления | Строй Советы
Оглавление:
Деревянные навесы: преимущества и недостатки
Деревянный навес для автомобиля: технология изготовления
Как сделать деревянный навес над крыльцом своими руками
Что такое навес? Если давать простое определение, то это то, что является защитой чего-либо от атмосферных осадков – дождя, снега, града и всего прочего, что может падать с неба. Навес можно построить над входной дверью, с его помощью можно защитить машину или просто стол во дворе частного дома. Его можно построить даже из разных материалов и при всем при этом он будет оставаться все тем же навесом. В этой статье вместе с сайтом stroisovety.org мы изучим деревянные навесы – рассмотрим их преимущества и самостоятельный монтаж.
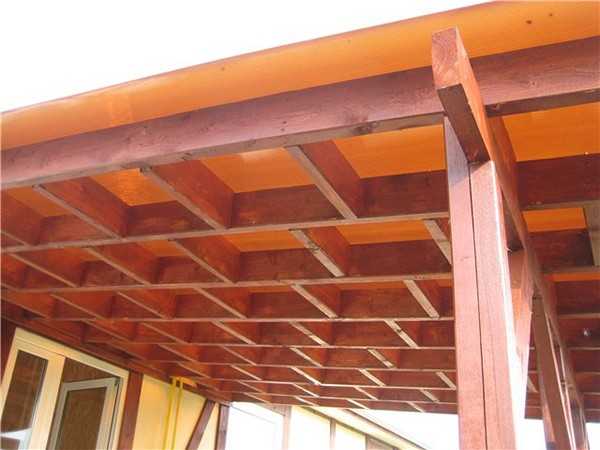
Деревянный навес к дому фото
Деревянные навесы: преимущества и недостатки
В принципе, навес можно изготовить практически из любого более или менее подходящего материала. В большинстве случаев это древесина или профильный металл, иногда кирпич в сочетании с металлом или деревом и какой-либо кровельный материал. Такой комбинированный подход к строительству подобных конструкций позволяет достичь некоторых преимуществ – например, большой срок эксплуатации или снижение бюджета на постройку навеса. К прочим достоинствам деревянных навесов можно отнести следующие нюансы.
- Самое главное – это надежность и долговечность. Если разобраться подробнее, то металл со своей подверженностью коррозии не является конкурентом древесине. Используя для ее пропитки современные материалы, древесину можно заставить служить на благо человека очень долгие годы.
- Эстетика и тепло природного материала. От металла и того же кирпича просто веет холодом, нет никакого уюта. По сути, даже автомобиль, находясь под таким навесом, будет чувствовать себя как не в своей тарелке.
- Простое изготовление, не требующее специального оборудования. Наши прадеды только с помощью одного топора возводили такие дома, а их умениям позавидуют даже современные строители. Если же говорить о деревянном навесе к дому, то тут вполне можно обойтись элементарной ножовкой и молотком.
- Дешевизна конструкции. В принципе, древесина стоит сравнительно недорого (дешевле, чем металл), а самостоятельные работы в денежном эквиваленте не измеряются. Кроме того, затевая изготовление навеса из стали, следует понимать, что кроме него дополнительно понадобится приобретать кровельный материал.
В принципе, из чего сделать навес, решать вам, я не собираюсь переубеждать вас в обратном. Нравится железо? Пожалуйста, делайте навес из железа и покрывайте его металлочерепицей или поликарбонатом. Я лишь расскажу о том, как построить навес из натурального природного материала – именно такие навесы отлично смотрятся на фоне сруба, расположенного среди деревьев на берегу тихой реки.
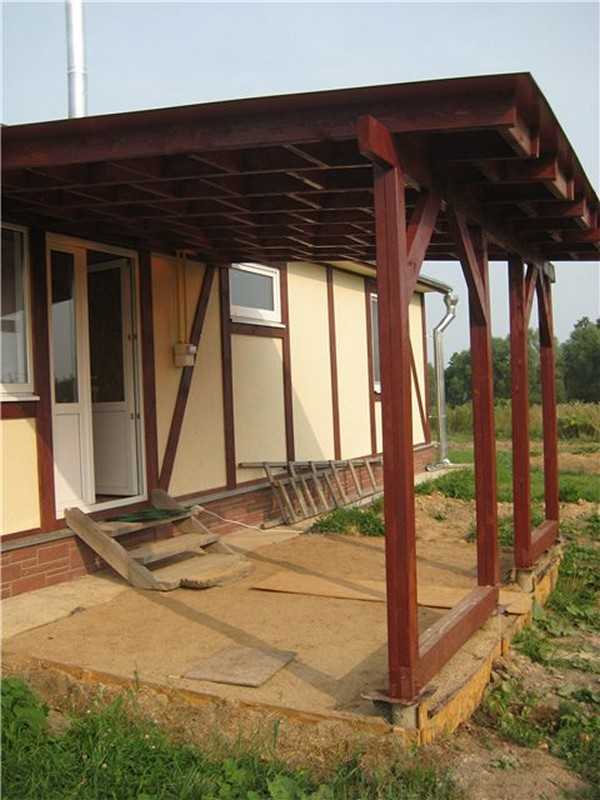
Деревянный навес над крыльцом фото
Деревянный навес для автомобиля: технология изготовления
Деревянный навес для автомобиля конструктивно немного отличается от навеса, изготовленного, скажем, над крыльцом. Эта разница заключается не только в размерах навеса, но и его массы и, как следствие, самой конструкции. Именно по этой причине мы рассмотрим два типа подобных изделий – прилегающих к дому и отдельно стоящих. Последние в большинстве случаев изготавливают для автомобилей, хотя бывает и по-другому (зачастую их пристраивают к дому). В любом случае, главной конструктивной особенностью автомобильных навесов являются стойки-опоры, которые призваны выдерживать вес навеса. Именно с них и нужно начать строительство.
Вне зависимости от того, где будет устанавливаться навес (рядом с домом или на расстоянии от него), как минимум понадобятся четыре такие стойки-опоры. Вообще здесь все зависит от массы навеса. Дерево – материал тяжелый, и практически всегда, кроме четырех угловых стоек, монтируются еще и промежуточные. Количество таких опор также в полной мере зависит от толщины этих стоек – если монтировать их из бруса сечением 100х100мм, то вполне можно обойтись и шестью штуками, а если в вашем распоряжении имеется брус 20х20мм, то и сотни таких дощечек может не хватить. Оптимальным считается использование в качестве опор бруса 50х50мм, также альтернативой может выступать доска сечением 40х80мм. Эти стойки (после предварительной обработки пропитками от влаги и гниения) закапываются в грунт согласно предварительно выполненной разметке.
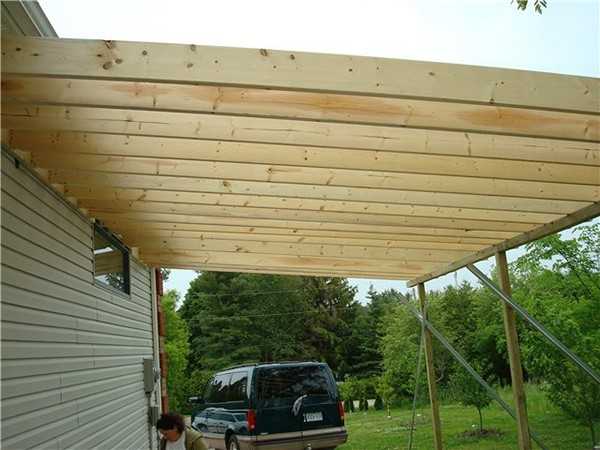
Деревянный навес для машины фото
Немаловажным элементом подобных конструкций являются горизонтальные перемычки – их еще иногда называют стяжками, так как они объединяют все стойки в единую прочную конструкцию. Такие перемычки располагаются по всему периметру навеса в его верхней части (под кровлей) и в нижней (с двух или трех сторон). Нижние перемычки одновременно служат изгородью, а в некоторых случаях и для крепления листового материала, например, профнастила, который выполняет функцию защиты от ветра. Изготавливают перемычки из бруса или доски – монтировать их можно как в накладку на стойки с наружной стороны навеса, так вставляя перемычки между ними.
Крыша навеса в большинстве случаев является односкатной и изготавливается, как и любая другая кровельная конструкция. Для ее изготовления можно использовать любой тип кровельного материала – покрыть навес из деревянного бруса можно как металлочерепицей, так и гибкой кровлей и даже ондулином. Из практики могу сказать только одно – на деревянных навесах лучше всего смотрится гонт (гибкая черепица), также можно рассмотреть вариант изготовления деревянной кровли. За такую крышу нужно быть готовым заплатить немало денег, даже в случае ее изготовления своими руками – уйдет много древесины, также будут расходы на ее столярную обработку. А в целом, такие навесы смотрятся великолепно.
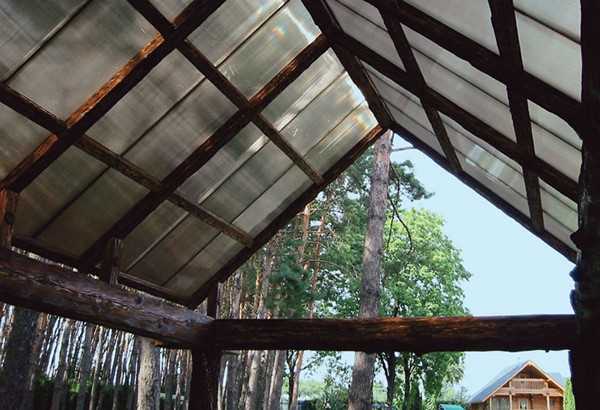
Как сделать деревянный навес для автомобилей
Как сделать деревянный навес над крыльцом своими руками
Деревянный навес своими руками над входной дверью дома делается немного иначе – хотя, если в его задачи входит накрыть крыльцо, то можно использовать и описанный выше принцип его изготовления. С ним мы уже немного разобрались и теперь уделим некоторое внимание небольшому навесу.
Основное его конструктивное отличие заключается в отсутствии стоек. В таких ситуациях кровля укладывается на большие кронштейны, которые называются откосами, раскосами или просто подвесными опорами. Изготавливаются они достаточно просто – по сути, вам придется сделать два больших треугольника из деревянного бруса. В эти треугольники обязательно должен быть заложен уклон, благодаря которому с навеса будет стекать дождевая вода, а зимой спадать накопившийся снег.
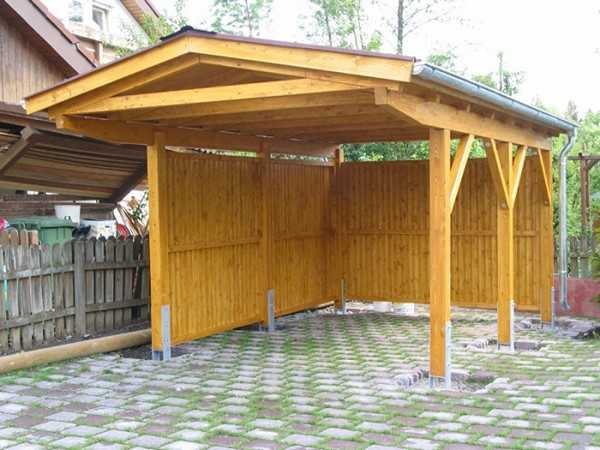
Как сделать деревянный навес своими руками
Изготовленные таким образом треугольные кронштейны крепятся над дверным проемом с помощью дюбелей или анкеров, после чего они соединяются в единую конструкцию горизонтальными перемычками. Одна из них устанавливается вдоль стены дома, а другая по краю кронштейнов – при необходимости монтируется и третья промежуточная горизонтальная перемычка, располагающаяся между крайними. Именно на эти перемычки впоследствии укладывается выбранный вами кровельный материал. Особое внимание при изготовлении подобных навесов нужно уделить его стыковке со стеной дома – чтобы вода не затекала в щель между стеной и навесом, место их соединения в обязательном порядке перекрывается специальным карнизом, один край которого врезается непосредственно в стену.
В этой статье мы рассказали только принцип, согласно которому делаются деревянные навесы. Следует понимать, что применять их можно по-разному – эти два способа можно комбинировать между собой или применять по отдельность. Данный принцип даже предусматривает использование различных материалов – придерживаясь его, можно построить не только навес из дерева, но и из металла, камня или каких-либо других подходящих материалов. Важно здесь только одно – навес должен быть прочным, надежным и уверенно выдерживать все природные катаклизмы. Поэтому лучше перестраховаться и заложить повышенный запас прочности.
Автор статьи Александр Куликов
stroisovety.org